How to Make Your Own DEF Fluid at Home Easily
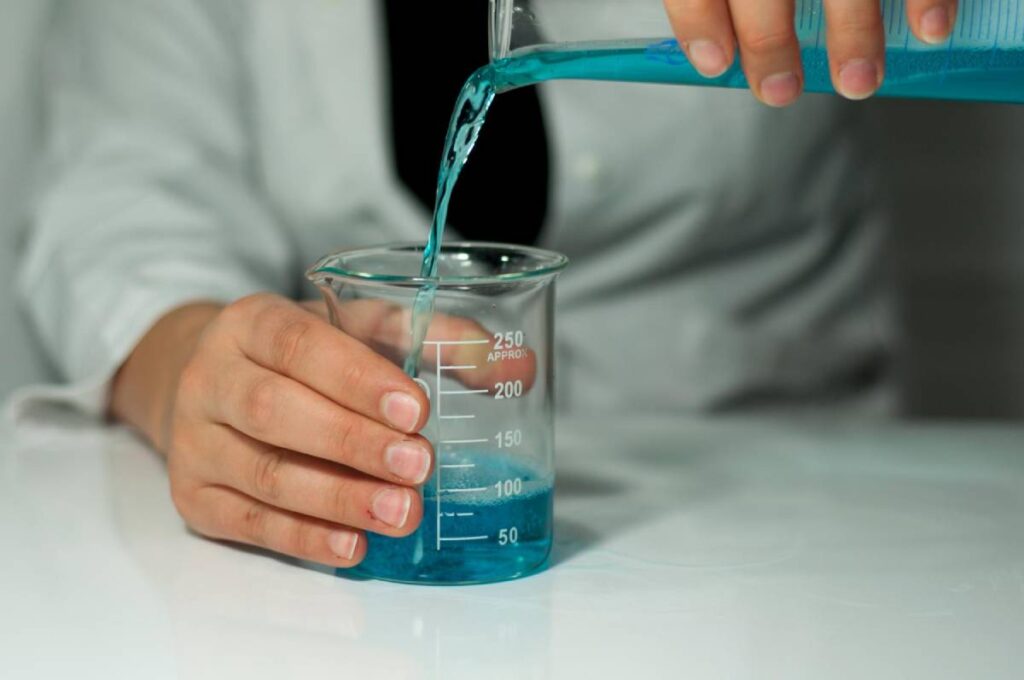
Understanding the Purpose of DEF Fluid Diesel Exhaust Fluid (DEF) plays a vital role in reducing harmful emissions in diesel engines. It is a non-toxic solution composed of 32.5% urea and 67.5% deionized water, used to convert nitrogen oxide (NOx) into harmless nitrogen and water through selective catalytic reduction (SCR). When you decide to make your own DEF fluid, it’s essential to understand this core function to maintain environmental standards. Commercial DEF products meet ISO 22241 specifications, ensuring purity and effectiveness. If you plan to make your own DEF fluid, these specifications should still guide your DIY process to avoid damaging the SCR system or voiding vehicle warranties. Knowing what DEF is and how it works helps ensure your homemade solution can perform its intended function without compromising engine performance or compliance. Ingredients Needed to Make Your Own DEF Fluid To make your own DEF fluid, you’ll need two primary components: pure, automotive-grade urea and deionized or distilled water. The concentration must be precise: 32.5% urea to 67.5% water. Any deviation could cause issues in the SCR system. Using technical or agricultural-grade urea is not recommended as it may contain impurities. When you make your own DEF fluid, purity is critical—both the urea and water must be free of contaminants. For water, avoid tap water due to its mineral content. Use only distilled or deionized water to prevent scaling or damage. These ingredients must be stored properly and mixed with clean equipment to maintain the required level of cleanliness and quality. Mixing Process and Safety Measures The process to make your own DEF fluid is simple but must be executed with care. Measure 325 ml of urea and 675 ml of deionized water to create one liter of DEF. Use a clean, chemical-resistant container to combine the ingredients. Stir slowly to dissolve the urea completely. Avoid direct contact with urea and always wear gloves and safety goggles during preparation. When you make your own DEF fluid, store the final product in a cool, shaded area away from sunlight. Exposure to heat or contaminants can degrade the solution’s effectiveness. Label the container and keep it sealed tightly. Always clean your tools thoroughly after use to maintain future batch quality and safety. Quality Control and Testing Considerations When you make your own DEF fluid, ensuring quality control is essential. Commercial DEF undergoes rigorous testing for concentration, contaminants, and performance. While home testing is limited, there are handheld DEF refractometers that can verify urea concentration. You can also check the pH level, which should range between 9.0 and 10.0. If you make your own DEF fluid frequently, investing in basic testing tools is recommended to prevent long-term damage to your vehicle. Remember that off-spec DEF can clog injectors, reduce SCR effectiveness, and even trigger error codes. Keeping your homemade DEF within standard parameters ensures both environmental compliance and engine reliability. Legal and Warranty Implications Before deciding to make your own DEF fluid, it’s important to consider legal and warranty-related consequences. Many vehicle manufacturers require ISO 22241-compliant DEF, and using unapproved fluids can void warranties. While it is technically legal to make your own DEF fluid for personal use, distributing or selling it without certification is not. Furthermore, emission compliance checks may fail if improper DEF is used, leading to penalties. Always read your vehicle’s manual and consult your manufacturer before switching to DIY solutions. The cost savings of homemade DEF should be weighed against potential risks and long-term impacts on your diesel engine and legal standing. Storage, Shelf Life, and Maintenance Once you make your own DEF fluid, proper storage is vital to maintain its effectiveness. DEF should be kept between 12°F and 86°F (–11°C to 30°C) and protected from sunlight. Freezing is reversible, but repeated cycles can affect the solution. When you make your own DEF fluid, label the container with the production date. Typically, DEF has a shelf life of one year if stored correctly. Avoid metal containers that can corrode and contaminate the fluid. Use HDPE or approved plastic tanks for safe storage. Periodically inspect the solution for sediment or discoloration, which are signs of contamination or degradation. Only use clean funnels and containers when transferring DEF to avoid introducing foreign particles. Cost Benefits and Environmental Considerations One of the main reasons people choose to make your own DEF fluid is cost. Commercial DEF can be relatively expensive over time, especially for fleet operators or those in remote areas. DIY production offers significant savings when done correctly. However, when you make your own DEF fluid, remember that quality should never be sacrificed for cost. From an environmental standpoint, maintaining DEF availability supports cleaner diesel emissions and aligns with sustainability goals. Producing it yourself also reduces transportation emissions associated with commercial supply chains. Yet, always ensure that your homemade DEF meets all quality standards to avoid negatively affecting your vehicle or the environment. Conclusion Learning how to make your own DEF fluid can be a practical and cost-effective solution for diesel vehicle owners. With the right ingredients, proper procedures, and a focus on quality control, it is possible to produce DEF at home that meets industry standards. However, caution must be exercised to avoid damaging sensitive emission systems or violating manufacturer warranties. The benefits—economic and environmental—are substantial when DIY DEF is done responsibly. As awareness around emission regulations grows, the ability to make your own DEF fluid offers flexibility and autonomy to those who need consistent access to this essential resource. Always prioritize safety, accuracy, and compliance to get the most out of your homemade DEF. Frequently Asked Questions Is it legal to make your own DEF fluid? Yes, for personal use it is generally legal, but selling it requires certification. Can I use tap water to make DEF? No, only distilled or deionized water should be used to avoid contamination. What is the ideal urea concentration in DEF? It should be exactly 32.5% urea to 67.5% water. Does homemade DEF void engine warranties? Yes, if it doesn’t meet
Make Your Own DEF Fluid: A Simple DIY Guide
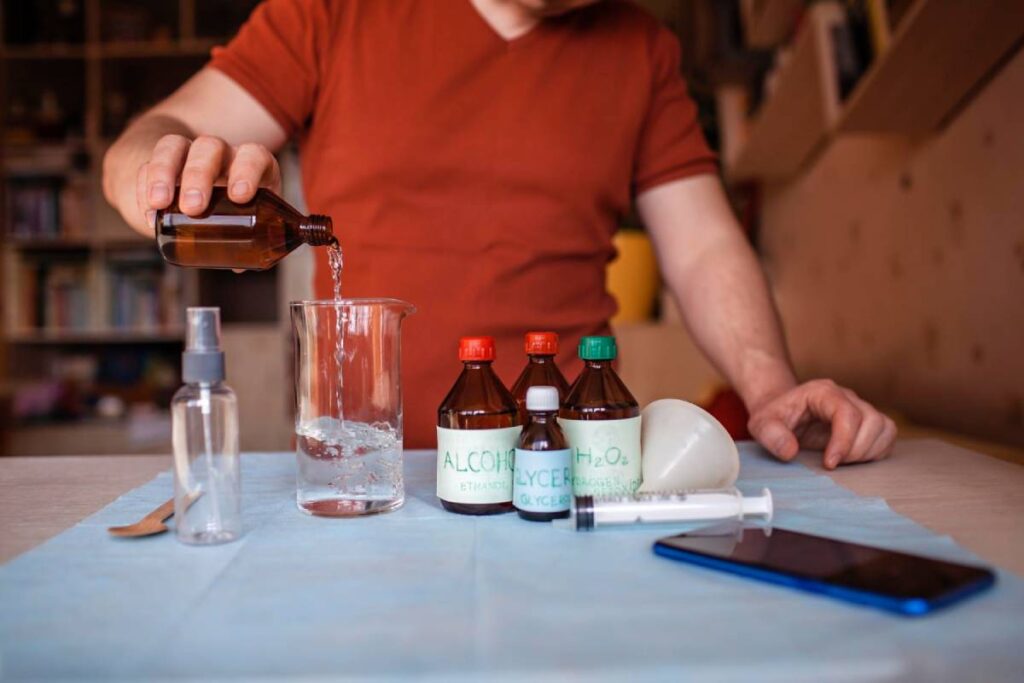
What Is DEF Fluid and Why It Matters Diesel Exhaust Fluid (DEF) is an essential component in modern diesel engines, used to reduce harmful nitrogen oxide emissions. It works in conjunction with the Selective Catalytic Reduction (SCR) system to convert toxic NOx gases into harmless nitrogen and water. When you choose to make your own DEF fluid, it’s important to understand the function and role it plays in protecting the environment. Creating a reliable alternative to commercial products requires knowledge of its chemical makeup—32.5% high-purity urea and 67.5% deionized water. If you intend to make your own DEF fluid, replicating this ratio accurately is vital for ensuring compatibility with your vehicle’s emission system. Understanding the purpose of DEF helps you appreciate why quality and consistency are crucial in your homemade version. Required Materials to Make Your Own DEF Fluid To make your own DEF fluid at home, you need access to two key ingredients: high-grade urea and deionized water. Agricultural or technical-grade urea may contain impurities, so it’s essential to use automotive-grade urea that meets the ISO 22241 standard. Similarly, regular tap water should be avoided due to the risk of mineral contamination. Only deionized or distilled water should be used. If you plan to make your own DEF fluid consistently, it’s worth investing in proper storage containers and clean mixing tools to maintain quality. Ensure all equipment is sanitized and that your workspace is free from dust or residue that could compromise the mixture. These precautions are critical to producing a safe, functional DEF solution. Step-by-Step Mixing Instructions The process to make your own DEF fluid is relatively straightforward but must be handled with precision. Start by measuring 325 milliliters of pure urea and 675 milliliters of deionized water. Pour the water into a clean container first, followed by the urea. Stir the mixture slowly and steadily until the urea is fully dissolved, ensuring an even blend. If you attempt to make your own DEF fluid using incorrect ratios or contaminated tools, you risk creating a solution that could damage your engine’s SCR system. Always mix in a well-ventilated area and wear gloves and safety glasses to protect yourself. Accuracy, cleanliness, and attention to detail are the keys to a successful DIY DEF batch. Quality Assurance and Testing Your DEF When you make your own DEF fluid, quality assurance becomes your responsibility. Commercial DEF products undergo strict laboratory testing for concentration and purity. While you may not have access to advanced lab equipment, handheld refractometers are affordable tools that can measure urea concentration and confirm it’s close to 32.5%. Regularly test pH levels as well; they should fall between 9.0 and 10.0. If you make your own DEF fluid regularly, investing in such tools will ensure your solution remains effective and safe for engine use. Without proper testing, homemade DEF could cause injector clogs, sensor failures, or costly engine repairs. Testing helps you catch and correct problems before they cause damage. Storage Guidelines and Shelf Life After you make your own DEF fluid, it’s crucial to store it correctly to maintain its effectiveness. DEF is sensitive to temperature and light. It should be kept between 12°F and 86°F (–11°C to 30°C) in a sealed, opaque plastic container made of HDPE material. Exposure to sunlight or extreme temperatures can degrade the fluid. When you make your own DEF fluid, label the container with the production date and avoid repeated freezing and thawing, which may reduce quality. Generally, DEF has a shelf life of one year under proper storage conditions. Inspect it periodically for discoloration or particulates that may indicate contamination. Clean storage practices are essential for maintaining integrity. Risks and Warnings You Should Know There are important risks associated when you make your own DEF fluid, especially if the fluid does not meet industry specifications. Incorrect concentration, impurities, or improper storage can damage your vehicle’s emission system and trigger dashboard warnings. If SCR components are compromised, repair costs can be substantial. Before you decide to make your own DEF fluid, review your vehicle’s warranty and consider whether using homemade DEF will void it. Moreover, regulatory implications may apply depending on your region. While personal use is generally permitted, commercial distribution is not. Knowing these risks in advance can help you take precautions and ensure a safer and more informed DIY experience. Advantages of DIY DEF Production Despite the risks, many users choose to make your own DEF fluid because of the potential for cost savings and accessibility. Commercial DEF can be expensive and harder to find in remote areas. Producing your own fluid reduces dependency on supply chains and gives you more control. If you make your own DEF fluid correctly, the results can match those of commercial products at a fraction of the cost. This can be especially beneficial for fleet operators or off-grid users. Moreover, there’s an environmental advantage—producing fluid locally reduces the carbon footprint associated with transportation. The key is ensuring your DIY efforts meet all necessary standards for safety and performance. Conclusion Choosing to make your own DEF fluid can be a practical and rewarding option for those seeking control over their diesel maintenance. With accurate measurements, proper materials, and attention to detail, DIY DEF can function similarly to commercial solutions. However, the risks of using subpar ingredients or deviating from industry standards must not be underestimated. If you decide to make your own DEF fluid, make sure you follow guidelines rigorously and test your solution frequently. Doing so ensures your engine remains compliant and efficient while avoiding costly damage. With careful preparation and consistent quality checks, homemade DEF can be both an economical and environmentally conscious solution for diesel engine users. Frequently Asked Questions Can I make my own DEF fluid legally? Yes, for personal use it is generally legal, but commercial sales are restricted. What type of urea should I use? Use only high-purity automotive-grade urea that meets ISO 22241 standards. Can I substitute tap water for deionized water? No, tap water contains
Obtaining a VDA License: A Comprehensive Guide
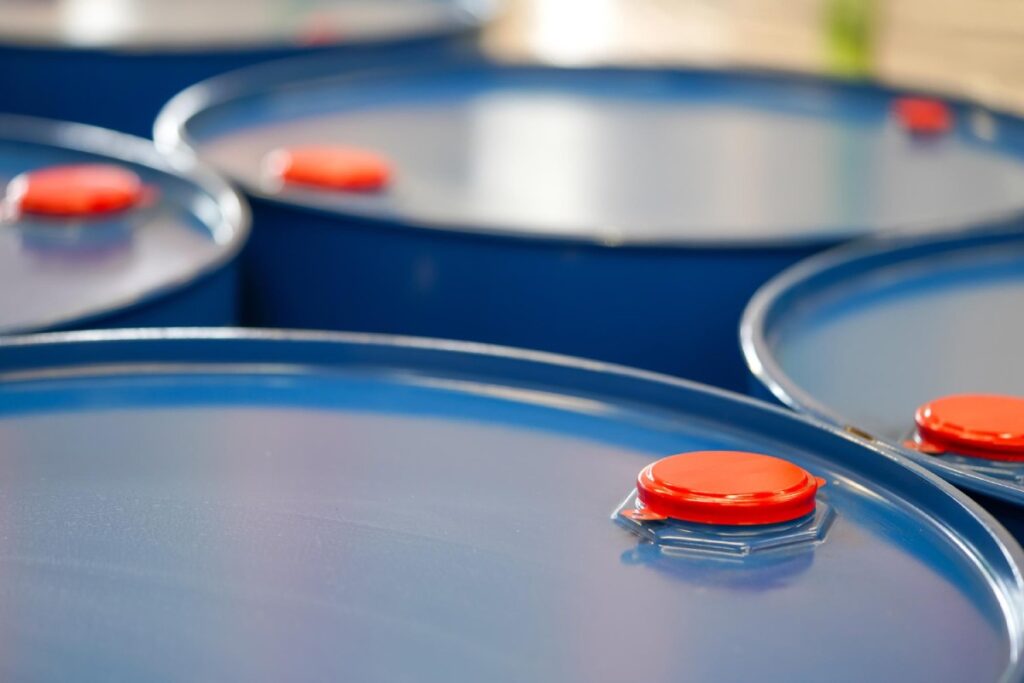
1. What is a VDA License? The VDA license (Verband der Automobilindustrie) is essential for companies aiming to comply with automotive industry standards. 2. Why is VDA Certification Important? Obtaining VDA certification demonstrates adherence to quality management and boosts credibility in the automotive market. 3. Who Needs a VDA License? Manufacturers, suppliers, and service providers in the automotive sector typically require a VDA license. 4. Prerequisites for Obtaining a VDA License Understanding the prerequisites like quality management systems (ISO 9001, IATF 16949) is crucial. 5. Step-by-Step Guide to Getting Licensed Follow these detailed steps to streamline your VDA licensing process and ensure compliance. 6. Cost and Duration of the Licensing Process Analyze the typical cost structure and timeline involved in acquiring your VDA license. 7. Key Documentation Required Ensure you prepare all mandatory documents such as audits, company profiles, and certifications ahead of time. 8. Common Challenges During the Application Identify common pitfalls and challenges to avoid delays in your licensing procedure. 9. Maintaining Your VDA Certification Learn how to maintain compliance with ongoing audits and quality checks post-certification. 10. Benefits of Holding a VDA License Discover the competitive advantages such as market recognition and improved partnerships that come with VDA compliance. Frequently Asked Questions (FAQs) How long does it take to receive a VDA license?Typically, it takes around 3-6 months depending on your preparedness and the complexity of your processes. What is the validity of a VDA certificate?A VDA certificate usually remains valid for 3 years, subject to periodic audits. Can a small company obtain a VDA license?Yes, businesses of all sizes can acquire a VDA license provided they fulfill the required quality standards. Is VDA licensing mandatory?While not legally mandatory, many major automotive manufacturers require their suppliers to have VDA certification. What happens if my company fails a VDA audit?You can usually address issues identified during audits within a specified timeframe and request a re-audit.
How is UAN32 Fertilizer Produced?
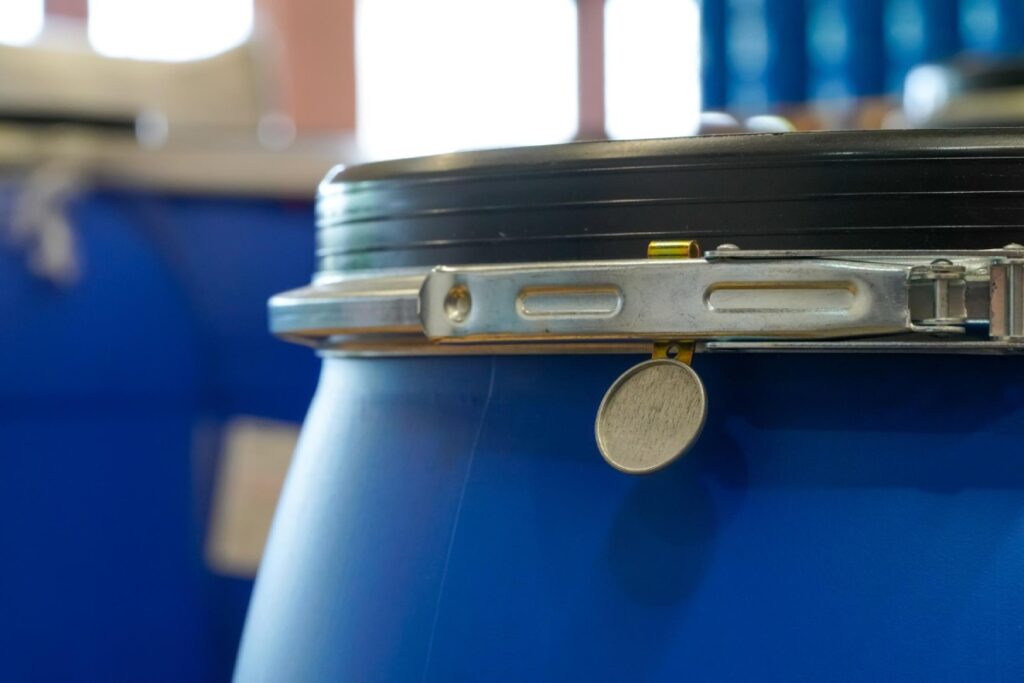
Understanding UAN32 and Its Importance UAN32 is a liquid nitrogen fertilizer commonly used in modern agriculture to enhance crop growth. It is a blend of urea, ammonium nitrate, and water, providing a balanced nitrogen source. The production process must adhere to strict quality standards to ensure effectiveness and environmental safety. Raw Materials Used in UAN32 Production The key ingredients in UAN32 production include high-purity urea, ammonium nitrate, and deionized water. Urea and ammonium nitrate provide the nitrogen content, while water serves as a solvent to create a stable liquid solution. These materials must be carefully measured to maintain the correct chemical composition. Mixing and Chemical Reactions During the production of UAN32, urea and ammonium nitrate are dissolved in water under controlled conditions. The solution is heated to promote complete dissolution, ensuring uniform distribution of nutrients. The mixing process prevents precipitation and enhances the stability of the final product. Filtration and Purification Filtration is essential in UAN32 production to remove impurities and solid particles. Advanced filtration techniques ensure that the final product is free from contaminants, preventing clogging in irrigation and spraying systems. Proper purification enhances the efficiency of nutrient absorption by crops. Storage and Handling Considerations Once produced, UAN32 must be stored in non-corrosive tanks to prevent contamination and chemical degradation. The solution should be kept at a stable temperature to avoid crystallization. Proper handling procedures ensure product quality and safety during transportation and application. Quality Control and Industry Standards Manufacturers follow stringent quality control measures to verify the composition and concentration of UAN32. Regular testing ensures compliance with agricultural regulations and industry standards. Adhering to these guidelines guarantees a reliable and effective fertilizer product. Application and Benefits of UAN32 UAN32 is widely used in precision agriculture due to its ease of application and rapid nutrient availability. Farmers can apply it through spraying systems or soil injection, ensuring efficient nitrogen uptake by plants. Its liquid form allows for better distribution, minimizing waste and maximizing crop yield. Conclusion The production of UAN32 involves precise blending of urea, ammonium nitrate, and water, followed by filtration and quality control measures. Proper storage and handling ensure the stability and effectiveness of the fertilizer. As a widely used nitrogen source, UAN32 supports sustainable farming practices by enhancing soil fertility and promoting healthy crop growth. FAQ What is UAN32 fertilizer? UAN32 is a liquid nitrogen fertilizer made from urea, ammonium nitrate, and water. How is UAN32 produced? UAN32 is produced by dissolving urea and ammonium nitrate in water under controlled conditions. What are the benefits of UAN32? UAN32 provides a balanced nitrogen source, enhances crop growth, and allows for easy application. How should UAN32 be stored? UAN32 should be stored in non-corrosive tanks at a stable temperature to prevent crystallization. Is UAN32 environmentally friendly? When used properly, UAN32 supports sustainable farming and minimizes nitrogen runoff. What crops benefit most from UAN32? UAN32 is commonly used for corn, wheat, and other cereal crops that require high nitrogen intake. How is UAN32 applied to fields? It can be applied through foliar spraying, soil injection, or mixed with irrigation water. Can UAN32 be mixed with other fertilizers? Yes, but compatibility testing should be done to avoid unwanted chemical reactions. What precautions should be taken when handling UAN32? Protective gear should be worn, and spills should be cleaned immediately to prevent environmental contamination. How does UAN32 compare to other nitrogen fertilizers? It is more versatile and easier to apply than solid fertilizers, offering better nutrient availability.
Improving Efficiency in UAN32 Production
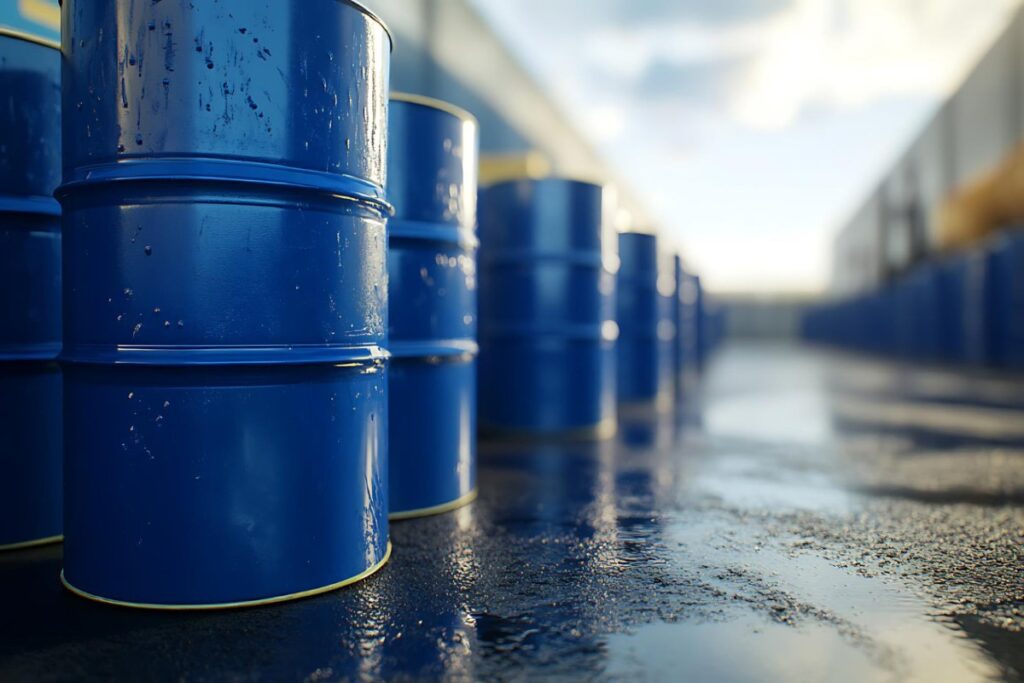
Understanding the Importance of Efficiency Efficiency in UAN32 production is essential for meeting agricultural demands while minimizing costs and environmental impact. By optimizing production processes, manufacturers can enhance product quality, reduce waste, and improve overall profitability. Optimizing Raw Material Usage One of the most critical factors in UAN32 production is the efficient use of raw materials. Ensuring the correct balance of urea, ammonium nitrate, and water helps maintain product stability and effectiveness. Reducing raw material waste contributes to cost savings and environmental sustainability. Enhancing Mixing and Dissolution Techniques Proper mixing and dissolution techniques play a key role in improving UAN32 production efficiency. Using advanced agitation systems ensures uniform distribution of ingredients, preventing crystallization and sedimentation. Temperature control during mixing further enhances product consistency. Implementing Advanced Filtration Methods Filtration is essential for removing impurities and ensuring high-quality UAN32. Advanced filtration methods, such as multi-stage filtration and membrane technology, improve product clarity and prevent clogging in agricultural application systems. Reducing Energy Consumption Energy efficiency is a major consideration in UAN32 production. Implementing energy-saving technologies, such as heat recovery systems and optimized process control, can significantly reduce operational costs. Sustainable energy sources further enhance efficiency and reduce the carbon footprint of production facilities. Quality Control and Process Monitoring Continuous monitoring of production parameters ensures the consistency and effectiveness of UAN32. Automated control systems and real-time data analysis help detect deviations early, allowing for quick corrective actions. Quality control measures also ensure compliance with industry standards and regulations. Storage and Distribution Improvements Efficient storage and distribution practices contribute to maintaining the integrity of UAN32. Using corrosion-resistant storage tanks and optimizing logistics reduce product loss and enhance supply chain efficiency. Proper handling procedures ensure safe and effective delivery to end-users. Conclusion Enhancing efficiency in UAN32 production involves optimizing raw material usage, improving mixing and filtration techniques, and implementing energy-saving strategies. By adopting advanced monitoring and quality control measures, manufacturers can produce high-quality UAN32 while reducing costs and environmental impact. FAQ Why is efficiency important in UAN32 production? Efficiency helps reduce costs, improve product quality, and minimize environmental impact. How can raw material usage be optimized in UAN32 production? By ensuring the correct balance of urea, ammonium nitrate, and water, manufacturers can minimize waste and enhance product stability. What role does mixing play in UAN32 efficiency? Proper mixing techniques prevent crystallization and sedimentation, ensuring a consistent and effective product. How does filtration improve UAN32 production? Filtration removes impurities, preventing clogging and ensuring high-quality UAN32. What energy-saving measures can be implemented in UAN32 production? Using heat recovery systems and optimizing process control can reduce energy consumption and operational costs. Why is quality control important in UAN32 production? Quality control ensures that UAN32 meets industry standards and remains effective for agricultural applications. How can storage and distribution efficiency be improved? Using corrosion-resistant storage tanks and optimizing logistics can reduce product loss and improve supply chain efficiency. Can automation improve UAN32 production efficiency? Yes, automated monitoring and control systems help detect issues early and maintain consistent production quality. What environmental benefits does efficient UAN32 production offer? It reduces waste, lowers energy consumption, and minimizes the overall carbon footprint of fertilizer production. How does efficient UAN32 production benefit farmers? Farmers receive a higher-quality product with improved nutrient availability, leading to better crop growth and yield.
Essential Equipment for UAN32 Production
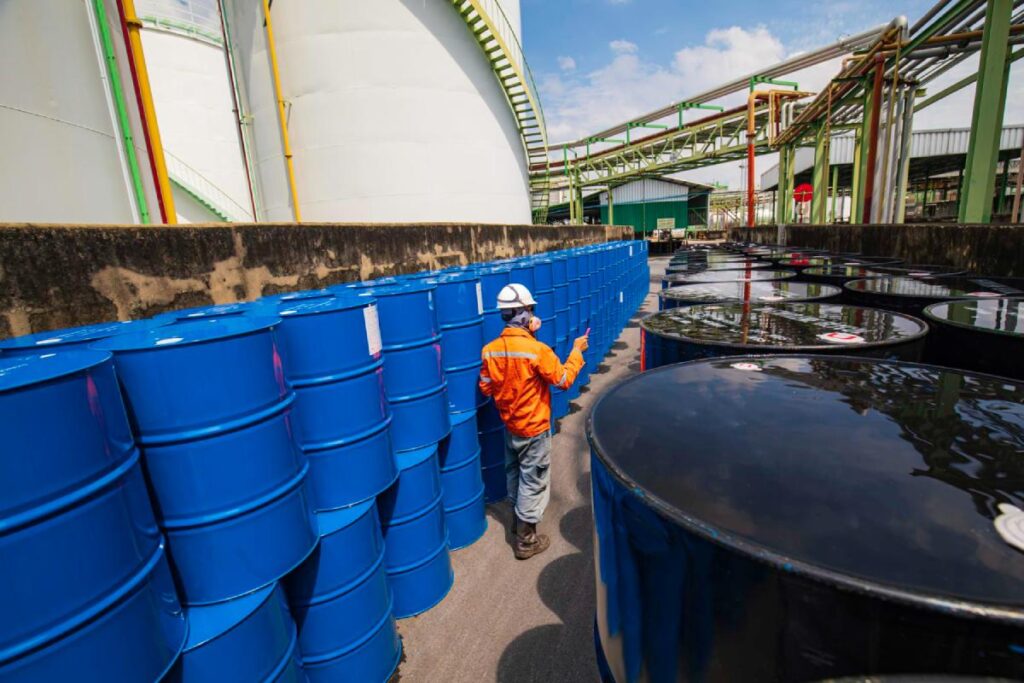
Introduction to UAN32 Production Equipment Producing UAN32 efficiently requires specialized equipment to ensure quality, consistency, and cost-effectiveness. The right machinery enhances production processes, minimizes waste, and meets industry standards for liquid fertilizer production. With the growing demand for UAN32, manufacturers must adopt advanced technologies to optimize production and maintain high standards. Mixing and Blending Systems Proper mixing is crucial in UAN32 production to achieve a homogenous solution. Advanced blending systems use high-speed agitators and automated dosing to ensure precise composition. Consistent mixing prevents crystallization and sedimentation, which can impact product quality. Additionally, using computer-controlled mixers can enhance precision and reduce human error, ensuring uniformity in every batch. Filtration and Purification Units Filtration is an essential step in UAN32 manufacturing to remove impurities that can clog distribution systems. Multi-stage filtration units help eliminate solid particles and contaminants, ensuring a high-purity final product. Some filtration systems include membrane technologies that provide ultra-purification, enhancing the overall efficiency and safety of UAN32. Storage and Handling Equipment Specialized storage tanks made from corrosion-resistant materials are necessary to store UAN32 safely. These tanks are designed to withstand chemical interactions and prevent contamination. Proper handling equipment, such as transfer pumps and pipelines, ensures smooth product movement within the facility. Automated handling systems can also enhance efficiency by reducing manual labor and ensuring precision in material transport. Heating and Temperature Control Systems Temperature control plays a vital role in UAN32 production, as fluctuations can lead to precipitation of salts. Heating systems maintain optimal production conditions, preventing crystallization and ensuring a stable final product. Some facilities implement advanced thermal insulation systems to minimize heat loss, reducing energy consumption and operational costs. Automation and Process Control Modern UAN32 production facilities utilize automated systems to monitor and control production variables. Automated dosing, real-time data tracking, and process adjustments help maintain consistency, efficiency, and regulatory compliance. Advanced SCADA (Supervisory Control and Data Acquisition) systems can improve monitoring capabilities, allowing operators to make real-time adjustments and optimize the entire production cycle. Quality Testing and Compliance Equipment Quality control is critical in UAN32 manufacturing. Advanced laboratory testing equipment ensures that each batch meets industry standards for nitrogen concentration, purity, and stability. Compliance with regulations guarantees a reliable and effective product. Regular audits and quality assessments help maintain consistent product integrity and prevent deviations that could affect agricultural performance. Energy-Efficient Production Technologies With increasing environmental concerns, many UAN32 production plants are adopting energy-efficient technologies. These include waste heat recovery systems, optimized pumping stations, and renewable energy sources to reduce the carbon footprint of fertilizer manufacturing. Investing in sustainability not only enhances operational efficiency but also helps companies meet global environmental regulations. Safety Measures and Risk Management Ensuring workplace safety in UAN32 production facilities is paramount. Installing proper ventilation systems, implementing spill containment protocols, and providing workers with protective gear are essential practices. Emergency shutdown systems and real-time monitoring sensors help prevent accidents and ensure a safe working environment. Conclusion Essential equipment for UAN32 production includes high-quality mixing systems, filtration units, storage solutions, and automation technologies. Investing in the right machinery enhances efficiency, maintains product integrity, and ensures compliance with agricultural standards. By adopting energy-efficient and safety-focused measures, manufacturers can improve operational sustainability while meeting the increasing demand for UAN32. FAQ What equipment is needed for UAN32 production? Essential equipment includes mixing systems, filtration units, storage tanks, and automation technologies. Why is mixing important in UAN32 production? Proper mixing ensures a uniform solution, preventing crystallization and improving product stability. How does filtration improve UAN32 quality? Filtration removes impurities, ensuring a high-purity product that meets industry standards. What storage conditions are ideal for UAN32? Corrosion-resistant tanks and controlled temperatures prevent degradation and contamination. How does automation enhance UAN32 production? Automated systems ensure precise mixing, real-time monitoring, and compliance with regulations. Why is temperature control necessary in UAN32 production? Maintaining optimal temperatures prevents precipitation and ensures a stable final product. What role does quality testing play in UAN32 manufacturing? Testing ensures that UAN32 meets nitrogen concentration and purity standards. How does proper handling equipment impact UAN32 production? Efficient pumps and pipelines prevent spills, contamination, and product loss. Can UAN32 production be optimized for energy efficiency? Yes, by using energy-efficient heating and automation systems, manufacturers can reduce costs. What are the main challenges in UAN32 production? Challenges include maintaining chemical balance, preventing impurities, and ensuring regulatory compliance.
Key Factors for a Successful Diesel Exhaust Fluid Plant
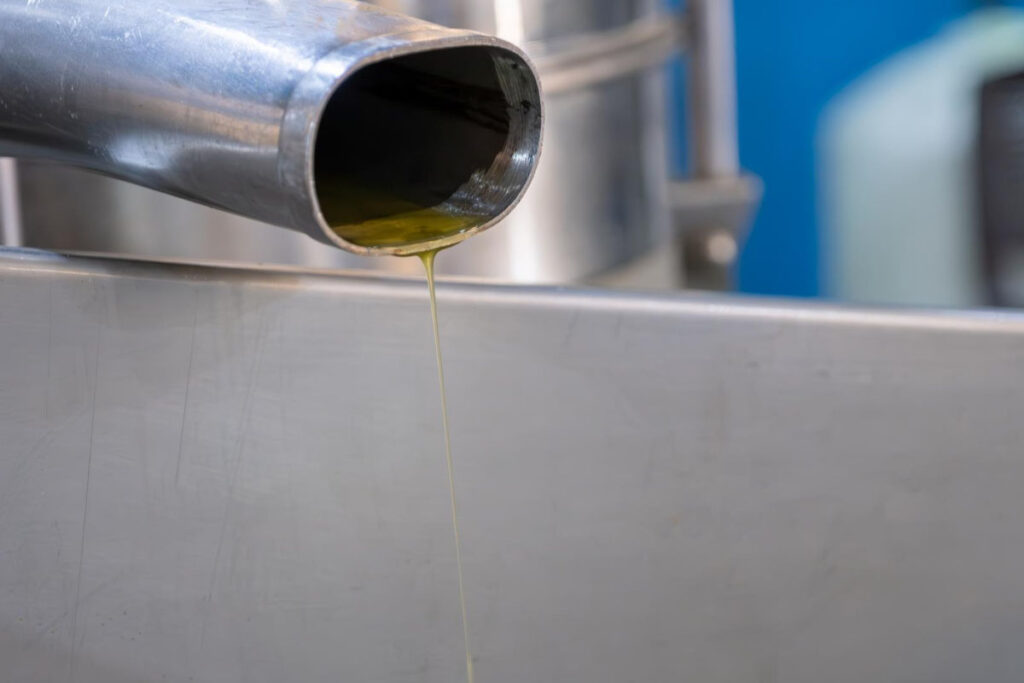
Choosing the Right Diesel Exhaust Fluid Making Machine The foundation of a successful diesel exhaust fluid plant starts with selecting a high-quality diesel exhaust fluid making machine. This machine is responsible for accurately mixing deionized water with high-purity urea to create DEF that meets ISO 22241 standards. When investing in a diesel exhaust fluid making machine, businesses should prioritize automation, precision, and reliability. Advanced machines with real-time monitoring, automatic shut-off features, and energy-efficient systems can significantly improve production efficiency and product consistency. Ensuring Compliance with Industry Regulations A diesel exhaust fluid plant must comply with strict industry regulations to ensure that the produced DEF meets required quality standards. DEF must have the correct urea concentration, be free from contaminants, and be stored in proper conditions. Investing in a certified diesel exhaust fluid making machine ensures that the production process adheres to industry guidelines. Regular quality control tests, documentation, and audits help businesses maintain compliance and avoid potential legal and financial issues. Optimizing the Production Workflow Efficiency is a crucial factor in running a profitable diesel exhaust fluid plant. The production workflow should be designed to minimize waste, streamline material handling, and maximize output. Integrating a state-of-the-art diesel exhaust fluid making machine into the production line helps maintain precise mixing ratios and reduces human errors. Implementing automated systems for material feeding, filtration, and storage further enhances productivity. Maintaining High-Quality Raw Materials Producing high-quality DEF requires the use of high-purity raw materials. A diesel exhaust fluid plant must source pure deionized water and technical-grade urea to ensure the final product meets industry standards. Using a top-tier diesel exhaust fluid making machine ensures that the urea and water are blended correctly without introducing contaminants. Regular testing and proper storage of raw materials are essential for maintaining product integrity. Effective Storage and Distribution Strategies Once DEF is produced, proper storage and distribution are essential to maintaining its quality. A well-designed diesel exhaust fluid plant should have temperature-controlled storage tanks and contamination-free dispensing systems. Choosing a diesel exhaust fluid making machine that integrates well with storage and packaging systems helps ensure seamless distribution. Efficient logistics planning further enhances supply chain reliability and customer satisfaction. Energy Efficiency and Cost Management Running a diesel exhaust fluid plant efficiently requires careful cost management and energy optimization. High electricity and water consumption can lead to unnecessary expenses, reducing overall profitability. Investing in an energy-efficient diesel exhaust fluid making machine helps lower operational costs. Regular maintenance, optimized workflows, and bulk purchasing of raw materials further contribute to cost savings and improved profit margins. Scalability and Future Growth Potential For long-term success, a diesel exhaust fluid plant should be designed with scalability in mind. As demand for DEF increases, businesses should be prepared to expand their production capacity. Using a modular diesel exhaust fluid making machine allows companies to scale production efficiently. Investing in infrastructure that accommodates future growth ensures sustained profitability and competitive advantage in the DEF market. Conclusion Establishing a successful diesel exhaust fluid plant requires careful planning, investment in high-quality equipment, and adherence to industry regulations. Choosing an advanced diesel exhaust fluid making machine, optimizing workflows, and ensuring high-quality raw materials contribute to consistent and efficient production. With a focus on cost management, compliance, and scalability, businesses can build a profitable and sustainable DEF production operation. Frequently Asked Questions What is a diesel exhaust fluid plant? A diesel exhaust fluid plant is a facility designed to produce DEF, a solution used in diesel engines to reduce harmful emissions. Why is compliance important for a diesel exhaust fluid plant? Compliance with ISO 22241 and other industry regulations ensures DEF purity, prevents engine damage, and avoids legal penalties. What role does a diesel exhaust fluid making machine play in production? A diesel exhaust fluid making machine accurately mixes urea and deionized water to create high-quality DEF that meets industry standards. How can I reduce operational costs in a diesel exhaust fluid plant? Using an energy-efficient diesel exhaust fluid making machine, optimizing production workflows, and buying raw materials in bulk help reduce costs. What are the storage requirements for diesel exhaust fluid? DEF should be stored in temperature-controlled tanks, away from contaminants and direct sunlight, to maintain its purity and effectiveness. How do I choose the best diesel exhaust fluid making machine? Look for a diesel exhaust fluid making machine with automation, real-time monitoring, and compliance with industry regulations. Can a diesel exhaust fluid plant be scaled up for future growth? Yes, by using a modular diesel exhaust fluid making machine and investing in scalable infrastructure, businesses can expand their production capacity. What quality control measures are necessary in DEF production? Regular testing, contamination prevention, and compliance with ISO standards ensure high-quality DEF production. How long does it take to set up a diesel exhaust fluid plant? The setup time depends on factors like facility size, regulatory approvals, and equipment installation. What is the expected return on investment for a diesel exhaust fluid plant? The ROI varies based on market demand, production efficiency, and operational costs, but most businesses see profitability within a few years.
How to Choose Reliable Diesel Exhaust Fluid Manufacturers
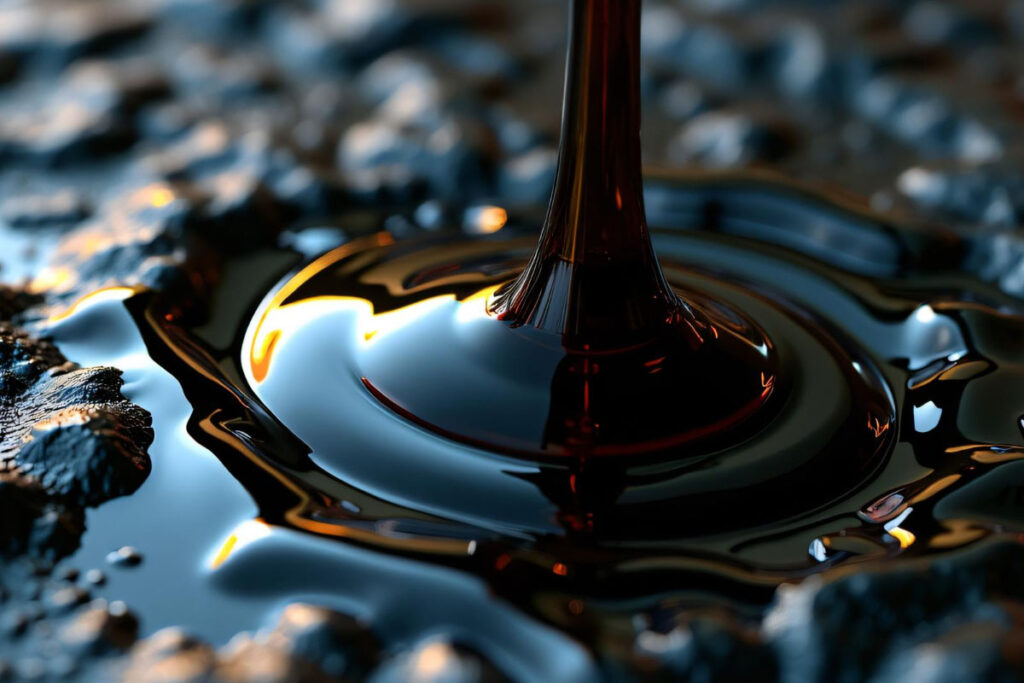
Understanding the Importance of Diesel Exhaust Fluid Manufacturers Diesel exhaust fluid manufacturers play a crucial role in helping businesses comply with stringent emissions regulations. Diesel Exhaust Fluid (DEF) is used in Selective Catalytic Reduction (SCR) systems to reduce nitrogen oxide emissions from diesel engines. Choosing the right manufacturer ensures that businesses receive high-quality DEF that meets ISO 22241 standards. A reliable diesel exhaust fluid manufacturer utilizes advanced production technology, such as a high-precision diesel exhaust fluid making machine, to ensure product purity and consistency. Partnering with a trusted manufacturer guarantees compliance, reduces operational risks, and helps businesses maintain an uninterrupted DEF supply. Key Characteristics of a Reliable Diesel Exhaust Fluid Manufacturer When evaluating diesel exhaust fluid manufacturers, certain characteristics set the best suppliers apart. The first factor to consider is their commitment to quality assurance. A top-tier manufacturer follows strict production standards and conducts frequent quality checks to maintain product integrity. Additionally, a reliable manufacturer invests in state-of-the-art equipment, such as an automated diesel exhaust fluid making machine, to produce DEF with the correct urea-to-water ratio. Manufacturers with industry certifications, transparent production processes, and strong distribution networks are more likely to provide dependable service. How Diesel Exhaust Fluid Manufacturers Maintain Product Quality Quality control is a top priority for reputable diesel exhaust fluid manufacturers. DEF must be free from impurities and produced with precise mixing techniques to ensure optimal performance in diesel engines. Using an advanced diesel exhaust fluid making machine, manufacturers can achieve consistent DEF purity. Regular laboratory testing, proper storage conditions, and compliance with ISO standards further enhance product quality. Businesses should verify whether a manufacturer adheres to these best practices before establishing a partnership. Factors to Consider When Choosing a Diesel Exhaust Fluid Manufacturer Several factors influence the selection of a reliable diesel exhaust fluid manufacturer. The most important aspects to evaluate include production capacity, supply chain reliability, regulatory compliance, and customer support. Manufacturers that use a high-quality diesel exhaust fluid making machine can produce DEF at scale without compromising quality. Additionally, businesses should assess the manufacturer’s reputation, delivery timelines, and ability to handle bulk orders efficiently. The Role of Diesel Exhaust Fluid Making Machines in Manufacturing A diesel exhaust fluid making machine is an essential component of any DEF manufacturing facility. This machine ensures that the correct proportion of deionized water and urea is mixed to meet industry standards. Reliable diesel exhaust fluid manufacturers use automated production equipment to eliminate human error, improve efficiency, and reduce contamination risks. Investing in a supplier that utilizes advanced machinery guarantees a higher-quality product and a more reliable supply chain. Verifying Compliance and Certifications of Diesel Exhaust Fluid Manufacturers Ensuring that diesel exhaust fluid manufacturers comply with industry regulations is critical for businesses. DEF must meet ISO 22241 standards to prevent engine damage and ensure environmental compliance. Manufacturers that invest in a high-performance diesel exhaust fluid making machine are more likely to meet these strict quality and purity standards. Businesses should request compliance certificates, quality assurance reports, and product test results before selecting a supplier. Benefits of Partnering with a Trusted Diesel Exhaust Fluid Manufacturer Working with a reliable diesel exhaust fluid manufacturer offers numerous advantages. High-quality DEF improves fuel efficiency, extends engine life, and ensures compliance with emission regulations. Additionally, manufacturers that use a cutting-edge diesel exhaust fluid making machine can provide consistent DEF supply, reducing risks associated with supply chain disruptions. Long-term partnerships with trusted manufacturers also lead to cost savings and better customer service. Conclusion Selecting the right diesel exhaust fluid manufacturer is essential for businesses that rely on DEF for regulatory compliance and engine efficiency. By evaluating quality control processes, production capabilities, and industry certifications, businesses can find a manufacturer that meets their needs. Manufacturers that use advanced diesel exhaust fluid making machine technology provide superior product quality, ensuring a stable and high-purity DEF supply. Frequently Asked Questions What do diesel exhaust fluid manufacturers do? Diesel exhaust fluid manufacturers produce DEF, a solution that reduces nitrogen oxide emissions in diesel engines. Why is choosing the right diesel exhaust fluid manufacturer important? A reliable diesel exhaust fluid manufacturer ensures high-quality DEF, regulatory compliance, and consistent product supply. What role does a diesel exhaust fluid making machine play in production? A diesel exhaust fluid making machine automates the blending of urea and deionized water, ensuring accurate DEF composition. How can I verify if a diesel exhaust fluid manufacturer meets industry standards? Check for ISO 22241 certifications, quality control processes, and compliance with industry regulations. What factors should I consider when selecting a diesel exhaust fluid manufacturer? Production capacity, compliance certifications, supply chain reliability, and use of a high-quality diesel exhaust fluid making machine are key factors. How does a high-quality diesel exhaust fluid making machine improve DEF production? It ensures precise mixing, reduces contamination risks, and improves overall production efficiency. Can poor-quality DEF damage diesel engines? Yes, low-quality DEF can lead to SCR system failures, increased emissions, and reduced engine performance. How often should DEF quality be tested? DEF should be tested regularly to ensure it meets ISO purity standards and remains free from contamination. What are the benefits of working with a large-scale diesel exhaust fluid manufacturer? Larger manufacturers offer better production capacity, stable supply chains, and more competitive pricing. Is buying DEF directly from manufacturers cost-effective? Yes, purchasing DEF directly from diesel exhaust fluid manufacturers reduces costs and ensures product quality.
Top Diesel Exhaust Fluid Manufacturers and Their Benefits
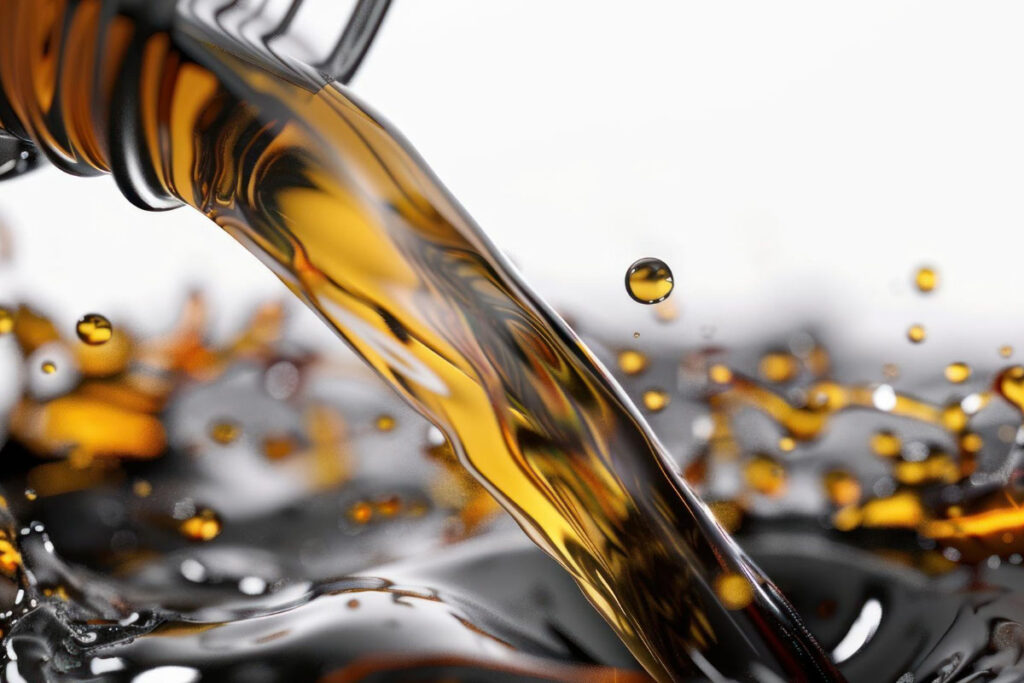
The Role of Diesel Exhaust Fluid Manufacturers in Emission Control Diesel exhaust fluid manufacturers play a crucial role in reducing harmful emissions from diesel engines. DEF is an essential component in Selective Catalytic Reduction (SCR) technology, which helps lower nitrogen oxide emissions. As global regulations on diesel emissions tighten, the demand for high-quality DEF continues to rise. To meet these demands, diesel exhaust fluid manufacturers must ensure that their products comply with ISO 22241 standards. This ensures that DEF remains free of contaminants, maintains proper urea concentration, and does not damage SCR systems. Utilizing an advanced diesel exhaust fluid making machine is essential for manufacturers to maintain consistent quality and meet regulatory requirements. Key Factors That Define a Reliable Diesel Exhaust Fluid Manufacturer Not all diesel exhaust fluid manufacturers provide the same level of quality and reliability. When selecting a manufacturer, businesses must consider several factors to ensure that they receive high-purity DEF that meets industry standards. A reputable manufacturer should use a state-of-the-art diesel exhaust fluid making machine to maintain consistent production quality. Additionally, the manufacturer should follow strict quality control measures, offer transparent compliance documentation, and provide efficient logistics and distribution services to ensure timely delivery of DEF. How Diesel Exhaust Fluid Manufacturers Maintain Product Quality Maintaining DEF quality is a priority for diesel exhaust fluid manufacturers. High-purity urea and deionized water must be used to produce a solution that meets regulatory requirements. Any contamination can compromise DEF performance and cause damage to diesel engines. By using a high-precision diesel exhaust fluid making machine, manufacturers can ensure accurate mixing ratios and prevent impurities. Regular laboratory testing, proper storage conditions, and advanced filtration systems further contribute to maintaining product integrity. Benefits of Choosing the Right Diesel Exhaust Fluid Manufacturer Selecting a reliable diesel exhaust fluid manufacturer offers several advantages. The most significant benefit is consistent product quality, which ensures optimal performance in diesel engines. High-quality DEF helps improve fuel efficiency and extends the lifespan of SCR systems. Additionally, working with a reputable manufacturer guarantees compliance with environmental regulations. A manufacturer that invests in advanced diesel exhaust fluid making machine technology can provide bulk production while maintaining high purity levels. Businesses that rely on a trusted supplier can also secure better pricing and more reliable supply chain operations. Technological Advancements in Diesel Exhaust Fluid Manufacturing Recent technological advancements have transformed the way diesel exhaust fluid manufacturers produce DEF. Modern production plants utilize fully automated diesel exhaust fluid making machine systems that enhance efficiency and reduce human error. Automated quality control systems, real-time production monitoring, and advanced filtration processes ensure that the final product meets strict purity requirements. These innovations allow manufacturers to increase production capacity while maintaining the highest quality standards, benefiting businesses that rely on DEF. Environmental and Economic Benefits of Diesel Exhaust Fluid Manufacturers Diesel exhaust fluid manufacturers play a vital role in reducing the environmental impact of diesel engines. By producing high-quality DEF, these manufacturers help lower nitrogen oxide emissions, improving air quality and contributing to sustainability initiatives. From an economic perspective, businesses that partner with a reliable diesel exhaust fluid manufacturer can lower operational costs by improving fuel efficiency and reducing maintenance expenses. Manufacturers that invest in energy-efficient diesel exhaust fluid making machine technology can also lower production costs, benefiting consumers through competitive pricing. How to Choose the Best Diesel Exhaust Fluid Manufacturer for Your Business Choosing the right diesel exhaust fluid manufacturer requires careful evaluation of several factors. Businesses should assess the manufacturer’s reputation, production capacity, compliance certifications, and commitment to quality assurance. Manufacturers that use an advanced diesel exhaust fluid making machine and adhere to strict regulatory guidelines are more likely to provide high-quality DEF. Additionally, businesses should consider supply chain reliability, delivery capabilities, and customer support services when selecting a DEF supplier. Conclusion Diesel exhaust fluid manufacturers play a crucial role in helping businesses comply with emission regulations while improving diesel engine efficiency. A reputable manufacturer invests in advanced diesel exhaust fluid making machine technology to ensure consistent product quality. By choosing the right manufacturer, businesses can secure a reliable DEF supply, optimize operational costs, and contribute to environmental sustainability. Frequently Asked Questions What do diesel exhaust fluid manufacturers do? Diesel exhaust fluid manufacturers produce DEF, a solution that reduces nitrogen oxide emissions in diesel engines. Why is it important to choose a reliable diesel exhaust fluid manufacturer? A reputable diesel exhaust fluid manufacturer ensures high-quality DEF, compliance with regulations, and a reliable supply chain. How is diesel exhaust fluid made? DEF is produced using a diesel exhaust fluid making machine that accurately blends high-purity urea with deionized water. What certifications should a diesel exhaust fluid manufacturer have? A reliable diesel exhaust fluid manufacturer should comply with ISO 22241 standards and other industry regulations. How do diesel exhaust fluid manufacturers ensure product quality? Manufacturers use a high-precision diesel exhaust fluid making machine, conduct laboratory tests, and implement strict quality control measures. Can diesel exhaust fluid be contaminated? Yes, contamination can occur if DEF is not properly stored or if low-quality production methods are used. What are the benefits of using high-quality DEF? High-quality DEF improves fuel efficiency, extends the life of SCR systems, and ensures compliance with emissions regulations. What is the role of a diesel exhaust fluid making machine in DEF production? A diesel exhaust fluid making machine automates the mixing process, ensuring accurate blending and consistent DEF quality. How can I verify the reliability of a diesel exhaust fluid manufacturer? Check for industry certifications, production capacity, and customer reviews to evaluate a diesel exhaust fluid manufacturer. Is it cost-effective to buy DEF directly from manufacturers? Yes, purchasing DEF directly from diesel exhaust fluid manufacturers can reduce costs and ensure consistent supply.
How to Make Your Own DEF Safely and Efficiently
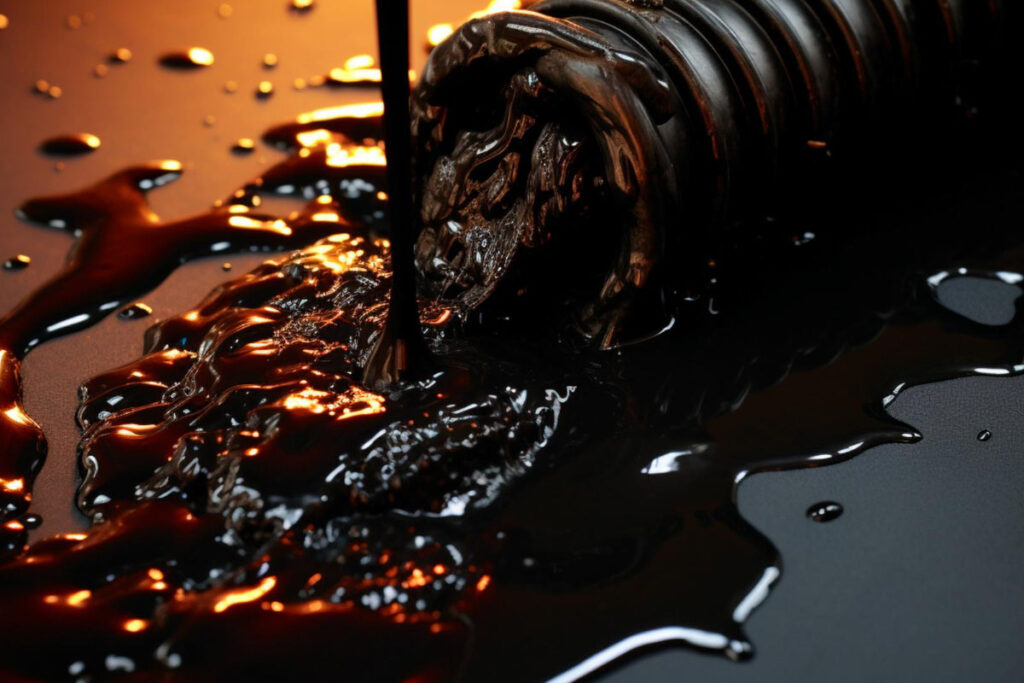
Understanding the Importance of Diesel Exhaust Fluid Diesel exhaust fluid (DEF) is a critical component in reducing harmful emissions from diesel engines. It is used in Selective Catalytic Reduction (SCR) systems to convert nitrogen oxides (NOx) into harmless water and nitrogen, helping vehicles meet environmental regulations. Making your own DEF can be a cost-effective solution, but it requires precision and high-quality equipment, such as a reliable diesel exhaust fluid making machine. Ensuring the correct formulation is essential to maintain engine efficiency and prevent damage to the SCR system. Key Ingredients Required to Make Your Own DEF The primary components of diesel exhaust fluid are high-purity urea and deionized water. The urea must be technical-grade (32.5% concentration) and free from impurities. Using impure water or lower-grade urea can result in DEF contamination, leading to engine malfunctions. A high-quality diesel exhaust fluid making machine ensures accurate blending of these ingredients to maintain compliance with ISO 22241 standards. Investing in proper raw materials and equipment helps ensure long-term reliability and performance. The Role of a Diesel Exhaust Fluid Making Machine Using a diesel exhaust fluid making machine is the most efficient way to produce DEF at scale. These machines automate the mixing process, ensuring the correct proportion of urea to deionized water, eliminating errors that could affect DEF quality. A high-quality diesel exhaust fluid making machine also includes filtration systems to remove impurities, preventing contamination. Automation improves accuracy, reduces human errors, and ensures consistent product quality, making it the best option for those looking to produce DEF reliably. Step-by-Step Guide to Making Your Own DEF Producing your own diesel exhaust fluid involves a precise process. Here’s how to do it properly: Source high-purity urea and deionized water. Use a calibrated diesel exhaust fluid making machine to mix the two ingredients in the correct 32.5% urea-to-water ratio. Ensure proper filtration to remove any potential contaminants. Store the DEF in a temperature-controlled, contamination-free environment. Following these steps ensures high-quality DEF that meets industry standards, protecting diesel engines from potential issues. Proper Storage and Handling of Homemade DEF Once you have successfully produced diesel exhaust fluid, proper storage and handling are crucial to maintain its quality. DEF is sensitive to temperature changes and contaminants, requiring specific storage conditions. Avoid exposing DEF to direct sunlight and extreme temperatures. Using sealed, non-metallic containers prevents contamination. A well-maintained diesel exhaust fluid making machine also helps ensure DEF remains pure throughout production and storage. Common Mistakes to Avoid When Making DEF There are several common mistakes that can compromise the quality of diesel exhaust fluid. One of the most significant errors is using tap water instead of deionized water, which introduces impurities and damages SCR systems. Another mistake is failing to use a proper diesel exhaust fluid making machine, leading to inaccurate mixing and inconsistent DEF quality. Ensuring correct storage conditions and conducting regular quality tests will help prevent these common pitfalls. Cost Savings and Benefits of Making Your Own DEF Producing your own diesel exhaust fluid can be a cost-effective alternative to purchasing pre-packaged DEF. By investing in a reliable diesel exhaust fluid making machine, businesses can significantly lower production costs while ensuring a steady supply. Long-term savings come from reducing reliance on external suppliers, avoiding price fluctuations, and maintaining control over DEF quality. For large-scale operations, in-house production leads to better efficiency, improved profitability, and environmental benefits. Conclusion Making your own diesel exhaust fluid is a viable option for businesses looking to save costs and maintain control over product quality. By using a high-quality diesel exhaust fluid making machine, following the correct formulation, and ensuring proper storage, you can produce DEF that meets industry standards. Investing in the right equipment and raw materials ensures long-term success and compliance with environmental regulations. Frequently Asked Questions Can I make my own diesel exhaust fluid at home? While possible, making diesel exhaust fluid requires precision, high-purity urea, and a diesel exhaust fluid making machine to ensure quality and compliance with industry standards. What is the correct ratio of urea to water in DEF? The standard DEF formula consists of 32.5% high-purity urea and 67.5% deionized water. Why is deionized water necessary for making DEF? Deionized water ensures that diesel exhaust fluid remains free from minerals and contaminants that could damage SCR systems. How long does DEF last after production? When stored properly, diesel exhaust fluid has a shelf life of about one year. What equipment do I need to make my own DEF? A diesel exhaust fluid making machine, high-purity urea, deionized water, and proper storage containers are essential. Can I use tap water to make DEF? No, tap water contains impurities that can degrade the quality of diesel exhaust fluid and damage the engine’s SCR system. How do I store DEF properly? Store diesel exhaust fluid in a temperature-controlled, sealed, non-metallic container away from direct sunlight. What happens if DEF is contaminated? Contaminated diesel exhaust fluid can cause engine malfunctions, increased emissions, and SCR system failures. Is making my own DEF cheaper than buying it? Yes, investing in a diesel exhaust fluid making machine allows businesses to reduce costs and ensure a consistent supply. What are the risks of making DEF incorrectly? Improperly mixed diesel exhaust fluid can lead to SCR system failure, regulatory violations, and costly engine repairs.