DEF vs. AdBlue: What Are the Technical Requirements for Production Machinery?
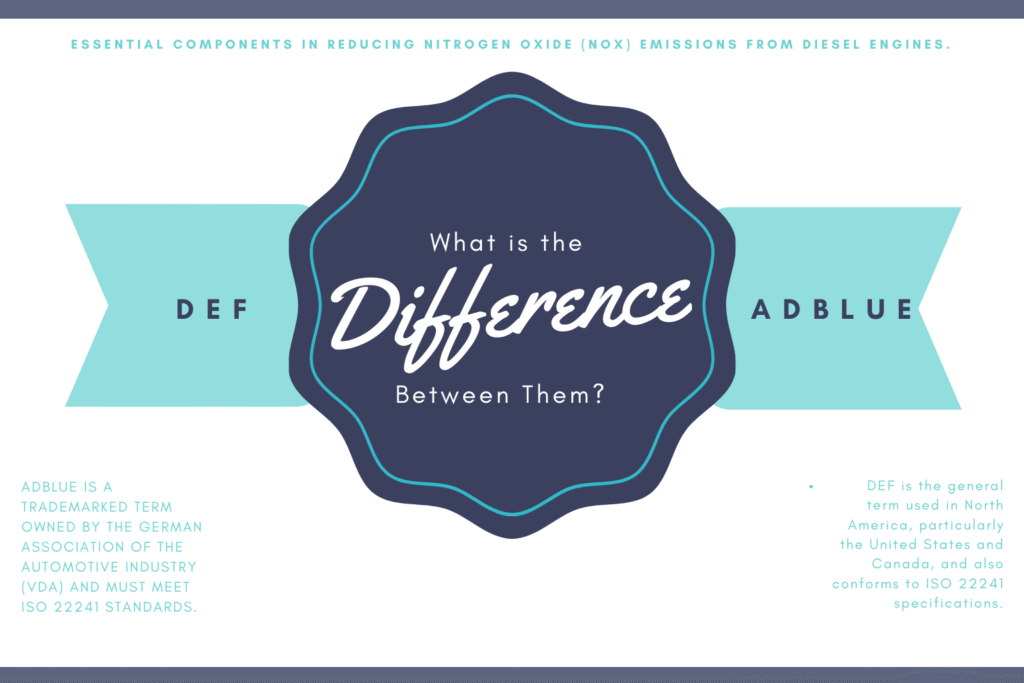
DEF vs. AdBlue: What Are the Technical Requirements for Production Machinery? As global emission regulations tighten, Diesel Exhaust Fluid (DEF) and AdBlue have become essential components in reducing nitrogen oxide (NOx) emissions from diesel engines. While the terms are often used interchangeably, there are subtle differences between them, especially in terms of branding and compliance. However, when it comes to the technical requirements for production machinery, precision and standardization remain universally critical. Understanding the Difference Between DEF and AdBlue At their core, both DEF and AdBlue are composed of a 32.5% high-purity urea solution in 67.5% deionized water. The key distinction lies in regional branding and certification: AdBlue is a trademarked term owned by the German Association of the Automotive Industry (VDA) and must meet ISO 22241 standards. DEF is the general term used in North America, particularly the United States and Canada, and also conforms to ISO 22241 specifications. So, from a chemical and functional standpoint, there is no difference between AdBlue and DEF. However, only products certified under the AdBlue license can legally carry the AdBlue name. Technical Requirements for Production Machinery Whether producing AdBlue or DEF, machinery must be specifically designed to maintain the purity and composition required by ISO 22241. Below are the key technical requirements: Urea Quality and Storage Use only automotive-grade urea with very low biuret and heavy metal content. Urea should be stored in closed, climate-controlled tanks to prevent contamination and moisture absorption. Equipment should include urea feeding pumps made from non-reactive materials (e.g., stainless steel or high-density polyethylene). Water Purification System Water must be demineralized to remove any ions, salts, or metals. Recommended purification methods include: Reverse Osmosis (RO) Ion Exchange Resins UV Sterilization (optional) Conductivity of the purified water should be below 0.5 µS/cm to comply with ISO standards. Blending Unit Accurate mixing is critical. Machinery should maintain a 32.5% urea to 67.5% water ratio with less than ±0.2% deviation. Use flow meters, conductivity sensors, and temperature controllers to monitor and adjust the blending process in real time. Blending tanks must be non-corrosive, ideally made of polypropylene or stainless steel. Automation and Smart Controls Modern DEF/AdBlue production lines should feature PLC (Programmable Logic Controller) systems for automation. Integration with IoT sensors and remote monitoring enables predictive maintenance and real-time quality assurance. Software should support data logging, batch tracking, and compliance reporting for audits. Filling and Packaging Equipment Filling systems must prevent contamination and maintain sterility throughout the process. Bottling machines, IBC (Intermediate Bulk Container) fillers, and tanker loaders should use closed-loop systems. Accurate volume control is essential to reduce waste and meet customer specifications. Material Compatibility All piping, valves, pumps, and tanks must be constructed from AdBlue/DEF-compatible materials. Avoid copper, brass, aluminum, and mild steel as they may react with the fluid and compromise its purity. Trusted Equipment Providers: Atmosfer Makina For companies seeking robust, compliant, and automated production solutions, Atmosfer Makina offers state-of-the-art DEF/AdBlue manufacturing systems. Their machines are designed specifically to meet ISO 22241 requirements, support remote access, and minimize human error in blending and bottling processes. For detailed technical consultation or to request a quote, you can contact Atmosfer Makina via: Mobile / WhatsApp: +90 541 947 0414 +90 539 549 05 12 Email: General inquiries: [email protected] Marketing & partnerships: [email protected] Technical support: [email protected] Why Purity Matters: The Impact of Contaminants on SCR Systems In DEF/AdBlue production, even microscopic impurities can have serious consequences. Contaminated fluid can clog injectors, damage the catalyst in Selective Catalytic Reduction (SCR) systems, and trigger vehicle fault codes. As a result, maintaining ultra-high purity is not optional—it’s essential. Production machinery must be designed to minimize contact with air, metals, and non-compatible materials. Additionally, regular cleaning protocols, closed-loop piping, and sterile filling equipment are all part of maintaining product integrity. Investing in precision equipment saves costs in warranty claims and protects your brand reputation. Batch vs. Continuous Production: Which Method Is Better for You? Choosing between batch and continuous production setups depends largely on your output volume, budget, and operational flexibility. Batch Production: Ideal for small to medium-scale operations. Easier to manage and allows frequent formula checks. Less initial investment. Continuous Production: Suitable for high-demand environments. Offers greater efficiency, consistency, and automation potential, but requires more advanced infrastructure. Companies like Atmosfer Makina offer scalable systems that can accommodate both models, making it easier to grow as your business expands. Maintaining ISO 22241 Compliance: Equipment Checklist To legally sell AdBlue or DEF under recognized standards, producers must comply with ISO 22241. Here’s a simplified checklist your equipment should meet: ✅ Demineralized water purification unit (RO or ion exchange) ✅ Corrosion-resistant tanks and piping (HDPE, stainless steel) ✅ Precision dosing system to maintain 32.5% urea concentration ✅ Flow meters, conductivity sensors, and temperature controllers ✅ Cleanroom-grade filling and packaging systems ✅ Secure storage with temperature control and UV protection ✅ Digital batch tracking and compliance reporting tools Failing to meet these standards may result in product rejection or regulatory penalties. Common Mistakes in DEF/AdBlue Production and How to Avoid Them Using tap water or semi-purified water – This increases mineral content and conductivity, leading to ISO non-compliance. Inadequate blending control – Manual mixing often results in improper ratios and poor product quality. Incorrect material selection – Using aluminum or copper in piping systems leads to contamination. Poor sealing during packaging – Open systems allow air and particles to enter, ruining batch purity. No data logging or batch documentation – Failing to track quality can result in liability during audits or customer complaints. Avoiding these mistakes is easier with modern, automated machinery. Atmosfer Makina’s systems are designed to address each of these issues proactively. Cost Optimization: How Automation Lowers Operational Expenses Though automation may seem like a major upfront investment, it significantly reduces operational costs over time by: 🔧 Minimizing labor through smart control panels and remote monitoring 🕒 Reducing downtime thanks to predictive maintenance alerts 📉 Preventing overuse of raw materials via precision metering ✅ Ensuring consistent product quality, avoiding reworks or recalls
Why Global Manufacturers Choose Turkish-Made AdBlue Machinery
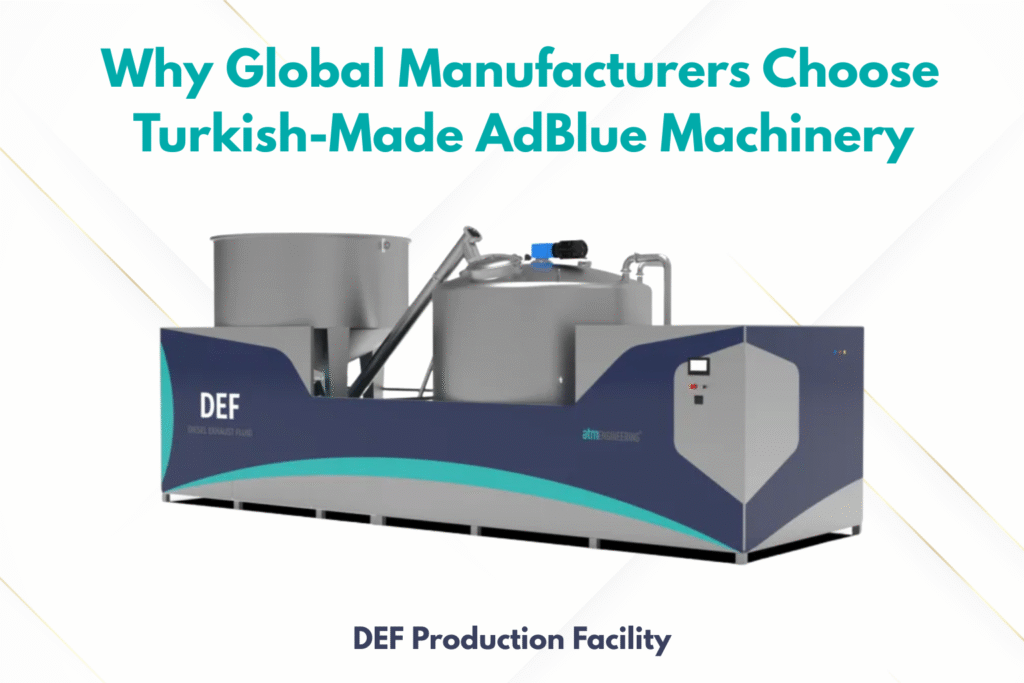
Why Global Manufacturers Choose Turkish-Made AdBlue Machinery In today’s competitive diesel exhaust fluid (DEF) and AdBlue market, manufacturers are under growing pressure to deliver consistent quality, maintain ISO 22241 compliance, reduce operational costs, and scale rapidly. With these challenges in mind, global producers are increasingly turning their attention to Turkish-made AdBlue machinery—and especially to trusted companies like Atmosfer Makina. So, what makes Turkey a rising hub for AdBlue production technology? And why is Atmosfer Makina becoming the go-to partner for manufacturers in Europe, the Middle East, Asia, and beyond? Let’s explore the key reasons behind this global shift. High-Quality Engineering with Competitive Pricing One of the biggest advantages of Turkish-made AdBlue machinery is its balance between European-grade engineering and cost-efficiency. Companies like Atmosfer Makina produce advanced systems that meet global quality standards, yet come at a fraction of the cost compared to Western manufacturers. Every unit manufactured by Atmosfer Makina is designed with: ISO 22241 compliance in mind Long-lasting, non-corrosive materials (HDPE, stainless steel) State-of-the-art sensors, PLC controls, and precision dosing technology Smart integration options such as IoT monitoring and remote access This combination of quality and affordability allows customers to achieve faster return on investment (ROI) while maintaining long-term operational reliability. Export-Focused Manufacturing and Global Support Unlike many local manufacturers that serve only domestic markets, Atmosfer Makina has built a strong reputation as an export-oriented producer, delivering machinery to clients in over 30 countries. Their systems are designed with international shipping, on-site setup, and remote technical support in mind. Clients benefit from: Multilingual documentation and manuals CE-certified systems for European markets Fast spare parts availability Online diagnostics and remote maintenance services This global mindset gives customers confidence that their Turkish-made AdBlue machinery isn’t just affordable—it’s truly world-class. Custom-Built Systems Tailored to Your Production Volume One size doesn’t fit all—especially in the AdBlue industry. Atmosfer Makina understands this and offers tailor-made production and filling lines that match your exact capacity and infrastructure needs. Whether you’re a small-scale distributor producing 2,000 liters per day, or a large fleet operator needing 50,000+ liters, Atmosfer Makina engineers scalable solutions, including: Batch or continuous production lines Fully automated filling stations (IBC, drum, bottle) Water purification systems (RO + deionization) Storage tanks with temperature and UV control Integrated labeling and packaging equipment Their flexible approach is one of the main reasons global manufacturers prefer Atmosfer Makina over larger, rigid European competitors. Strong After-Sales and Technical Support Many international companies hesitate to purchase industrial machinery from abroad due to concerns about technical support. Atmosfer Makina eliminates that fear by offering: Direct WhatsApp support: +90 541 947 0414 and +90 539 549 05 12 Dedicated technical email line: [email protected] Video call assistance and real-time diagnostics Preventive maintenance training for local teams Their responsive service ensures that downtime is minimized, and your production keeps running smoothly—no matter where you’re located. Continuous Innovation and R&D Investment While some suppliers rely on outdated designs, Atmosfer Makina continuously evolves its product range. The company invests in new technologies such as: AI-driven fault detection Solar-integrated AdBlue systems Modular production lines for easier expansion ERP and SCADA integration This forward-thinking approach has earned them the trust of OEMs, logistics firms, fuel station chains, and chemical producers worldwide. Proven Track Record and International References It’s not just about promises—Atmosfer Makina has a growing list of international success stories. From Europe to Africa, and from the Gulf countries to Central Asia, many clients have standardized their AdBlue operations with Atmosfer Makina’s machines. With hundreds of satisfied customers and repeat orders, the company has proven its value and reliability in global markets. Frequently Asked Questions (FAQ) Is Turkish-made AdBlue machinery really reliable for long-term use? Yes. Turkish manufacturers like Atmosfer Makina have proven their reliability through years of export experience and hundreds of satisfied clients worldwide. The company uses industrial-grade components, corrosion-resistant materials, and smart control systems that meet international standards. Their machinery is built not only to comply with ISO 22241 but also to withstand long-term, heavy-duty operation. Many customers have been using the same equipment for 5+ years with minimal maintenance thanks to robust engineering and continuous technical support. How does Atmosfer Makina support international clients after the sale? Atmosfer Makina offers one of the most comprehensive after-sales support services in the industry. Clients receive multilingual manuals, live video assistance for installation and troubleshooting, and can directly reach the technical team via WhatsApp or email. Preventive maintenance schedules, online diagnostic tools, and fast international shipping of spare parts ensure minimal downtime. The company takes pride in staying accessible long after the machinery is delivered—something many competitors overlook. 📱 WhatsApp Support: +90 541 947 0414 / +90 539 549 05 12 📧 Technical Contact: [email protected] Can Atmosfer Makina customize a machine based on our specific production needs? Absolutely. Unlike many large-scale equipment suppliers that only offer standardized models, Atmosfer Makina specializes in tailor-made solutions. Whether you require batch or continuous production, large-scale or small-scale output, IBC or bottle filling stations—every machine can be custom-built. The engineering team collaborates with you to analyze your space, budget, water source, and output goals to ensure the system fits your facility perfectly. They also offer modular designs, making it easy to scale up in the future. What certifications and standards do Atmosfer Makina machines comply with? All production units and auxiliary systems are manufactured in compliance with ISO 22241, the global standard for AdBlue quality and handling. In addition to this, Atmosfer Makina’s machines carry CE certification for safe use within the European Union and are built with materials like stainless steel, HDPE, and PP to prevent urea crystallization or contamination. The systems are also compliant with environmental and workplace safety standards, giving you peace of mind during audits or certifications. What are the advantages of buying AdBlue machinery from Turkey compared to Germany or China? Purchasing from Turkey, and specifically from Atmosfer Makina, offers a unique combination of advantages: European-quality engineering with a more affordable price tag Geographical proximity to both Europe and the Middle East,
What to Expect from Atmosfer Makina at Automechanika Istanbul 2025
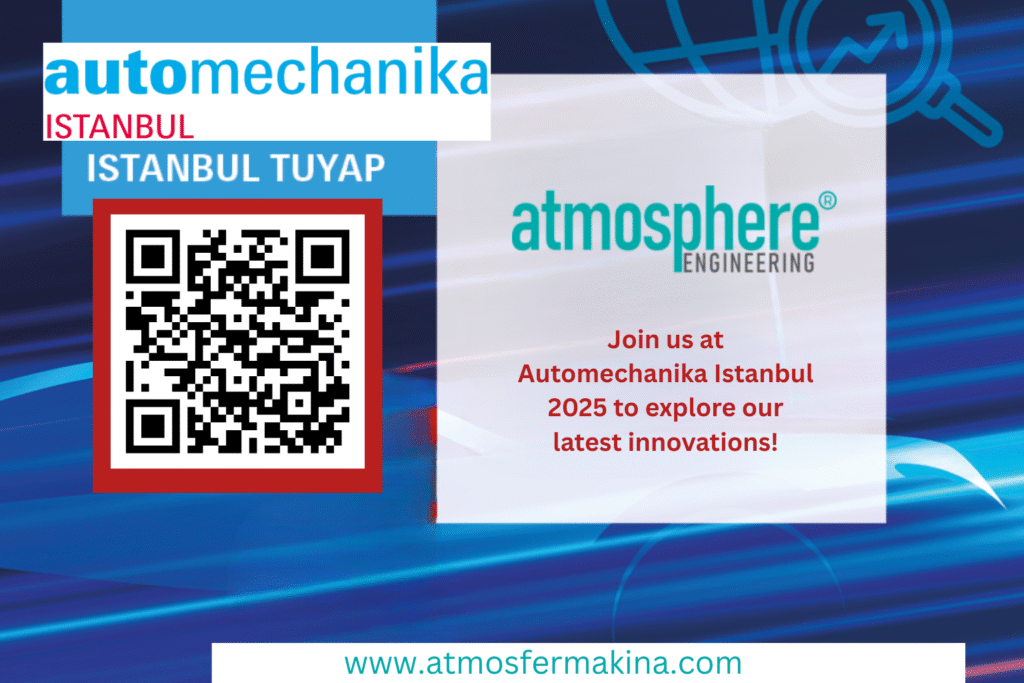
What to Expect from Atmosfer Makina at Automechanika Istanbul 2025 The countdown has begun for one of the most anticipated automotive industry events of the year—Automechanika Istanbul 2025. As always, this prestigious international fair will bring together thousands of companies, industry leaders, innovators, and buyers under one roof. Among the key exhibitors to watch closely is Atmosfer Makina, a leading Turkish manufacturer of AdBlue and DEF production systems. If you’re planning to attend Automechanika this year, here’s why a visit to Atmosfer Makina’s booth should be high on your list. A Global Reputation in AdBlue Machinery Innovation With a proven track record of supplying high-quality, ISO 22241-compliant AdBlue machinery to over 30 countries, Atmosfer Makina has become synonymous with precision engineering, customer-oriented design, and reliable after-sales service. At Automechanika 2025, the company will be showcasing not just machines—but complete, smart, scalable production systems developed for the future of DEF and AdBlue manufacturing. Whether you’re a fleet owner, fuel distributor, chemical producer, or investor, this is your opportunity to see why Atmosfer Makina continues to be the preferred choice of global manufacturers. Live Demonstrations of Cutting-Edge Equipment One of the highlights of Atmosfer Makina’s booth will be live demonstrations of their best-selling systems, including: Compact AdBlue production units for small-to-medium scale businesses Fully automated filling and capping systems for bottles, IBCs, and drums Smart PLC and touchscreen control panels with IoT integration Water purification modules using RO and deionization technologies Filling line innovations designed to reduce product loss and boost speed These live demos will give attendees a hands-on feel of the precision, user-friendliness, and build quality that define Atmosfer Makina’s product range. New Launches and Technology Reveal Automechanika 2025 will also be the platform where Atmosfer Makina unveils its latest developments in the AdBlue production sector. Expect to see: Modular systems for easier expansion and relocation Solar-integrated production units for off-grid operations AI-powered system diagnostics for predictive maintenance Multi-format filling solutions for enhanced flexibility These innovations are designed with one goal in mind: future-proofing AdBlue production for businesses operating in diverse environments and regulatory landscapes. Meet the Experts Behind the Machines Visitors to the Atmosfer Makina stand will have the opportunity to meet with the company’s engineers, project managers, and international sales team. These experts will be available for one-on-one consultations, helping you: Analyze your current production needs Design a custom DEF/AdBlue plant layout Discuss shipping, installation, and training processes Explore pricing, ROI, and after-sales options Whether you’re just starting or looking to upgrade, Atmosfer Makina will guide you through every step of the process. Free Resources and Giveaways for Visitors To make the experience even more rewarding, Atmosfer Makina will offer exclusive materials and gifts at their booth, including: A printed technical catalog of their full machine range Case studies and project samples from around the world Branded giveaways such as USB drives, notebooks, and accessories A chance to schedule a free remote demo after the event Early visitors might also secure a special show-only discount on machinery packages. Frequently Asked Questions (FAQ) What products will Atmosfer Makina showcase at Automechanika Istanbul 2025? Atmosfer Makina will exhibit AdBlue mixing, filling, and packaging systems, smart control units, and modular production lines. Where will Atmosfer Makina be located at the event? The company will be at Hall 14, in the AdBlue and environmental technologies section. Is it necessary to book an appointment to meet with a representative at the fair? Yes, it is recommended to schedule an appointment in advance for one-on-one meetings. Visit Atmosfer Makina’s official website for more details. What innovative technologies will Atmosfer Makina introduce at the event? They will present IoT-based monitoring panels, energy efficiency reporting, and remote access-enabled systems. Are there any special offers available at Atmosfer Makina’s stand? Visitors can expect exclusive price offers, previews of new models, and opportunities for direct consultation with engineering experts. Need More Info Before the Show? Reach out to Atmosfer Makina directly with your questions, meeting requests, or technical needs: 📞 WhatsApp / Mobile: +90 541 947 0414 or +90 539 549 05 12 📧 General: [email protected] 📧 Marketing Inquiries: [email protected] 📧 Technical Support: [email protected]
What to Look for When Choosing AdBlue Production Equipment in 2025
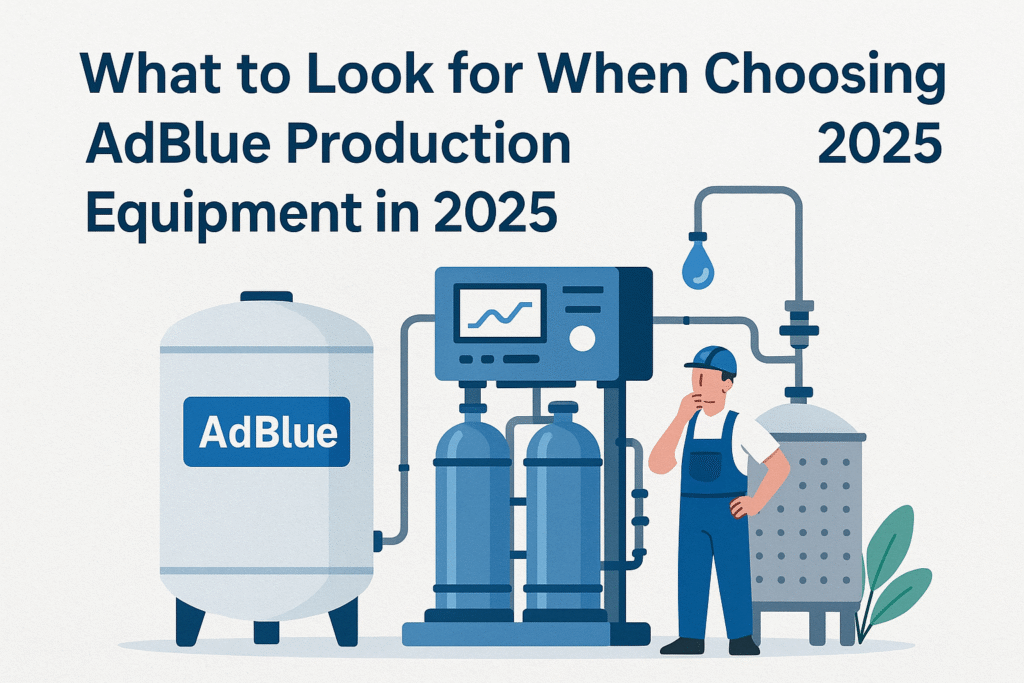
In an era where environmental regulations are becoming increasingly stringent, the importance of efficient and reliable AdBlue production cannot be overstated. With the rise of diesel vehicles that rely on SCR (Selective Catalytic Reduction) systems to meet emission standards, the demand for high-quality AdBlue is higher than ever. Whether you’re starting a new AdBlue manufacturing facility or upgrading an existing one, choosing the best AdBlue equipment is critical for ensuring long-term success. In this AdBlue machinery buyer guide, we will break down the essential factors to consider when investing in AdBlue production technology in 2025 — including why partnering with a trusted supplier like Atmosfer Makina can make all the difference. Why AdBlue Production Equipment Matters More Than Ever The AdBlue production process is not as simple as mixing chemicals. It requires precision dosing, temperature control, contamination prevention, and strict adherence to ISO 22241 standards. Subpar equipment can lead to low-quality output, system failures, or worse — legal and environmental consequences. Choosing the right AdBlue production machinery ensures: Consistent product quality Compliance with international standards Operational efficiency and scalability Long-term cost savings Let’s explore the most important criteria to evaluate when shopping for AdBlue equipment in 2025. 1. Compliance with ISO 22241 Standards Your top priority should be ensuring the equipment complies with ISO 22241, the international standard for AdBlue (also known as AUS 32) production and handling. This includes: Proper material selection (e.g., stainless steel tanks, Teflon-coated components) Accurate urea concentration control Protection from contamination (dust, oils, etc.) Temperature and storage guidelines Companies like Atmosfer Makina specialize in turnkey AdBlue plant solutions that are built entirely around ISO 22241 compliance, ensuring your product will meet the requirements for diesel vehicle engines worldwide. 2. Modular vs. Fully Integrated Systems In 2025, you’ll find a variety of AdBlue production system configurations, including: Modular systems: Scalable and customizable, ideal for businesses expecting growth or those with limited space. Fully integrated systems: All-in-one setups with mixing, filtration, and packaging in one compact unit. Each option has its own advantages. Modular systems allow for phased investment, while integrated systems can streamline operations. Atmosfer Makina offers both options and provides professional consultation to help determine the best fit for your specific needs. 3. Production Capacity and Scalability Think ahead. Will your production volume remain static, or will you scale operations in the next 3–5 years? Many manufacturers make the mistake of buying smaller, less expensive machinery only to replace it within a year. Look for: Adjustable flow rate Automated dosing systems Options to upgrade tank size or add filling lines For example, Atmosfer Makina’s AdBlue production lines can be tailored for capacities ranging from 1,000 to 20,000 liters per day, and their modular designs allow for seamless expansion as your business grows. 4. Automation and User Interface In 2025, the best AdBlue equipment comes equipped with user-friendly interfaces, real-time monitoring, and remote diagnostics. Smart technology is no longer optional; it’s a necessity for operational efficiency. Features to consider: PLC control panels with touchscreen interfaces Automated alarms for pH imbalance, temperature changes, or contamination Cloud-based monitoring dashboards Atmosfer Makina integrates modern automation into all its systems, allowing operators to monitor and adjust parameters with minimal training and maximum reliability. 5. Filtration Systems and Contamination Control One of the most critical steps in AdBlue production technology is the filtration phase. Even microscopic impurities such as dust particles, lubricants, or metal residues can render the final product unusable — or worse, damage a vehicle’s SCR system. A robust filtration system should include: Multi-stage filtration (typically 5μm, 1μm, and 0.5μm filters) Closed-loop systems to prevent airborne contamination UV sterilization (optional but highly recommended for extended shelf life) Atmosfer Makina ensures every production line is equipped with industrial-grade filtration systems that meet ISO 22241-3 requirements, significantly reducing the risk of product recalls or quality complaints. 6. After-Sales Support and Spare Parts Availability Even the most advanced machinery needs regular maintenance and occasional part replacements. A key factor in your purchasing decision should be the level of after-sales support provided by the manufacturer. Look for: Availability of local technical service teams Quick shipment of spare parts Remote troubleshooting and diagnostics Detailed operation and maintenance manuals Atmosfer Makina stands out by offering dedicated customer support in both English and Turkish, ensuring your production doesn’t face unnecessary downtime. Their global spare parts distribution ensures fast delivery to Europe, the Middle East, Africa, and Asia. 7. Energy Efficiency and Environmental Considerations As sustainability becomes a top business priority, selecting energy-efficient AdBlue machinery helps reduce operating costs and your carbon footprint. Features that contribute to a greener production line: Low-energy mixers and pumps Smart sensors that minimize energy consumption Wastewater recycling and reduction technologies Atmosfer Makina places sustainability at the heart of its designs. Their systems are optimized for low power usage and can be integrated with solar panels or other renewable energy sources. 8. Why Choose Atmosfer Makina? With over a decade of experience in fluid production technologies, Atmosfer Makina is a reliable partner for businesses seeking turnkey AdBlue plant solutions in 2025. Here’s what sets them apart: ✅ Custom-built systems tailored to your production needs ✅ Full ISO 22241 compliance from raw material handling to packaging ✅ High-end automation with real-time control features ✅ Fast delivery and on-site installation worldwide ✅ Long-term technical support and spare parts availability Whether you’re a first-time investor or a large-scale producer, Atmosfer Makina offers scalable and efficient AdBlue production equipment that grows with your business. Frequently Asked Questions (FAQ) Q1: How long does it take to install a complete AdBlue production line? A: Installation timelines vary depending on the system size, but Atmosfer Makina typically completes delivery and setup within 6–8 weeks. Q2: Can I start with a smaller capacity and upgrade later? A: Yes. Modular systems from Atmosfer Makina are designed for easy scalability. You can expand your capacity as demand increases. Q3: What kind of training is provided for staff? A: Hands-on training is included with every installation, along with multilingual manuals and remote
Why ISO 22241 Compliance Matters for AdBlue Production Machinery
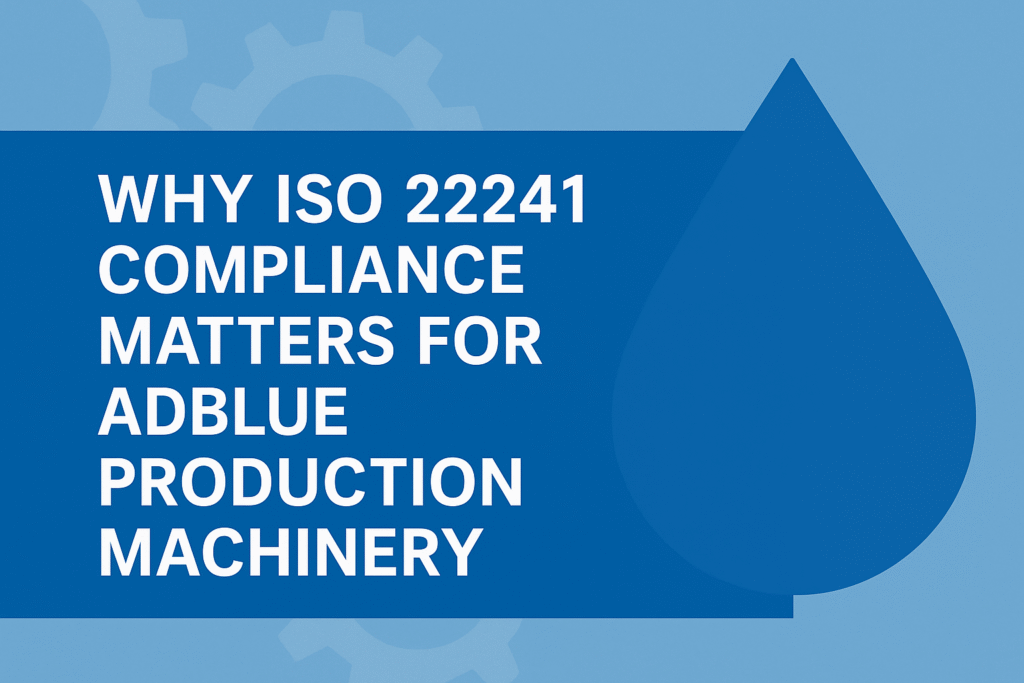
As global emission regulations become increasingly stringent, AdBlue—also known as Diesel Exhaust Fluid (DEF)—has emerged as a critical component in reducing nitrogen oxide (NOx) emissions from diesel engines. Used across a wide range of vehicles, from passenger cars to heavy-duty trucks, AdBlue plays a central role in the Selective Catalytic Reduction (SCR) process. However, not all AdBlue is created equal. To ensure the effectiveness of SCR systems and to avoid damage to vehicle components, the production, handling, and storage of AdBlue must meet strict quality criteria. That’s where ISO 22241 comes in—a set of internationally recognized standards designed to guarantee the safety, purity, and compatibility of AdBlue. For manufacturers of AdBlue production machinery, ensuring compliance with ISO 22241 is not just a technical requirement—it’s a business necessity. This blog explores why ISO 22241 compliance is vital for equipment design, plant operations, and long-term business sustainability. What is ISO 22241? ISO 22241 is a multi-part international standard developed to ensure the quality and handling of AdBlue (or AUS 32 – Aqueous Urea Solution). It governs every aspect of the DEF lifecycle—from chemical composition to production machinery and storage containers. ISO 22241 Includes: Part 1: Quality requirements for AdBlue fluid itself Part 2: Test methods to verify composition and purity Part 3: Handling, transport, and storage guidelines Part 4: Requirements for refilling interfaces (like nozzles and ports) Part 5 (Draft in some regions): Quality assurance in manufacturing systems The goal of ISO 22241 is to maintain the chemical integrity of AdBlue and prevent contamination that can impair SCR systems in diesel vehicles. Why Compliance Matters for Machinery Manufacturers 1. Purity Assurance AdBlue must be free of metals, minerals, and organic substances that can damage SCR systems. Machinery that doesn’t meet ISO 22241 may introduce contaminants during blending, filling, or packaging. Non-compliant risks include: Crystallization in the vehicle’s exhaust system Reduced NOx reduction efficiency Costly engine repairs 2. System Compatibility Machinery used in AdBlue production must be constructed from approved materials that do not react with the urea solution. ISO 22241 outlines materials such as: High-grade stainless steel (e.g., AISI 316L) Specific plastics (e.g., PE-HD, PP, or PTFE) 3. Global Market Access Clients and distributors in Europe, the Middle East, Asia, and North America often require ISO 22241 certification as a baseline. Manufacturers who fail to comply may be locked out of regulated markets or lose tenders to compliant competitors. Atmosfer Makina’s Commitment to ISO 22241 Standards As a leading manufacturer of AdBlue production lines and turnkey plants, Atmosfer Makina ensures that all machinery complies with ISO 22241 standards from design through delivery. Their systems are tailored to protect the chemical purity and meet the structural requirements needed for international distribution. Features of ISO 22241-Compliant Machinery by Atmosfer Makina: Blending Units with Sealed Stainless-Steel Tanks Prevent contamination and maintain temperature control Automated Filling Lines with Closed-Loop Sensors Detect impurities and ensure batch consistency CIP (Clean-in-Place) Systems Allow internal cleaning without dismantling, reducing downtime and human error Material Certificates for Contact Components Each part in contact with AdBlue is certified for compliance Atmosfer Makina’s team continuously trains its engineers and project managers on evolving standards to ensure clients remain ahead of environmental and technical regulations. Designing and Building ISO 22241-Compliant AdBlue Machinery Designing AdBlue production machinery that meets ISO 22241 requirements is more than selecting a few compliant materials. It involves a detailed understanding of the standard, proactive design strategies, and strict quality assurance at every step. In this part, we’ll break down the key engineering and operational practices necessary to ensure your AdBlue production facility is fully ISO-compliant. 1. Material Selection: Start with Compatibility The materials used in any machinery that comes into contact with AdBlue must resist chemical degradation, prevent contamination, and not leach harmful substances into the fluid. According to ISO 22241, materials must be non-reactive with aqueous urea solutions. Approved Materials Include: Stainless Steel AISI 304L / 316L: Used in tanks, mixers, and piping. High-Density Polyethylene (PE-HD): Often used for pipework and fittings. Polypropylene (PP) and PTFE (Teflon): Common in valves, seals, and flexible hoses. Pro Tip: Avoid using materials like copper, brass, and zinc—they can catalyze urea degradation and introduce heavy metals into the fluid. 2. Sanitary Design: Preventing Contamination at Every Stage Contamination control is at the heart of ISO 22241. That’s why Atmosfer Makina implements sanitary design principles into every machinery component. Key Design Features: Smooth interior surfaces: Minimize urea crystallization and biofilm buildup. Closed-loop mixing systems: Eliminate air exposure and reduce impurity risks. Hygienic pumps and valves: Use self-draining designs with no dead zones. 3. Blending and Dosing Systems: Precision and Consistency Accurate dosing of pharmaceutical-grade urea and demineralized water is essential for maintaining the AdBlue 32.5% concentration ratio. Deviations can result in non-compliance and malfunctioning SCR systems. Atmosfer Makina’s Blending Technologies: Flow meters and sensors calibrated for urea density and temperature. Real-time feedback systems to adjust water/urea ratio on the fly. Batch recording and traceability for each production cycle. 4. Filling, Packaging, and Labelling: Compliant Down to the Details Packaging processes must also conform to ISO 22241 standards. Even if the fluid is compliant, poor packaging can lead to contamination or mislabeling. Compliance Essentials: Filling heads with no-drip, contactless designs. Anti-static, UV-resistant containers for long-term stability. Labels must include correct terminology (e.g., “AdBlue®”, “AUS 32”), production date, batch number, and storage instructions. Atmosfer Makina integrates automated filling lines with tamper-evident caps and programmable label applicators, ensuring accuracy and traceability in every unit. 5. Quality Control & Testing: The Final Line of Defense ISO 22241 Part 2 outlines testing methods to confirm the chemical composition and purity of AdBlue. Production machinery must support easy sampling, lab integration, and contamination checks. QC Tools Integrated by Atmosfer Makina: On-site conductivity and refractive index meters Microbiological testing stations Automated data logging systems for QA audits and export reports Conclusion: Build Smarter, Safer, and Compliant with Atmosfer Makina ISO 22241 is not just a standard—it’s a gateway to product reliability, customer
How to Set Up an AdBlue Production Line: Step-by-Step Guide for 2025
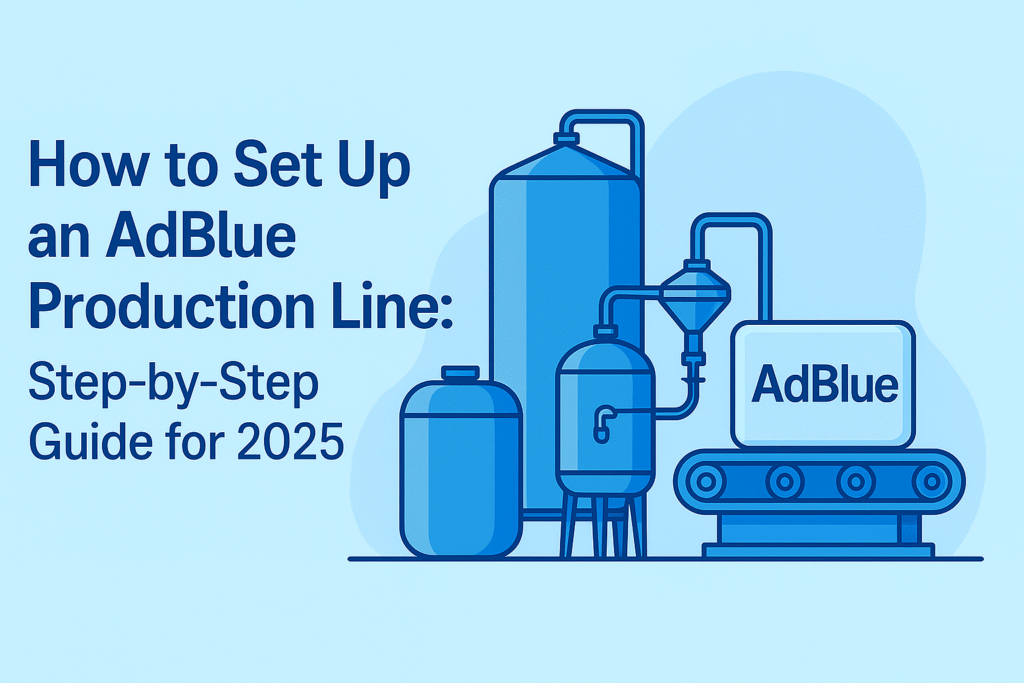
Why AdBlue Production Is a Smart Investment in 2025 How to Set Up an AdBlue Production Line As environmental regulations become increasingly stringent across the globe, diesel vehicle manufacturers and fleet operators face growing pressure to reduce harmful emissions. AdBlue—a high-purity urea solution used in Selective Catalytic Reduction (SCR) systems—is central to this transition. For entrepreneurs, industrial firms, and distributors aiming to enter the clean fuel sector, establishing an AdBlue production line is not only an environmentally responsible move but also a highly lucrative one. Whether you’re planning to serve a local market or scale internationally, setting up a reliable and compliant AdBlue plant is now more accessible than ever thanks to innovations in machinery and automation. This comprehensive, step-by-step guide—brought to you by Atmosfer Makina, a leading provider of turnkey AdBlue plants—walks you through everything from planning and equipment selection to production optimization and quality assurance. Step 1: Understanding What AdBlue Is Before diving into the technical setup, let’s clarify what AdBlue is and why it’s critical. What is AdBlue? AdBlue is a 32.5% aqueous urea solution that reduces harmful NOx (nitrogen oxide) emissions in diesel engines via the SCR process. It is also known as Diesel Exhaust Fluid (DEF) and is used in both commercial and passenger vehicles. Why is it important in 2025? Due to Euro 6 standards in Europe and similar emission laws across North America, Asia, and the Middle East, AdBlue demand is surging. Manufacturers, transport companies, and logistics providers are rapidly transitioning to SCR systems—meaning the global need for high-quality AdBlue is accelerating. Step 2: Market Research & Feasibility Before investing in equipment, facilities, or staff, a solid understanding of the AdBlue market landscape is essential. Key Questions to Answer: What is the current and projected demand for AdBlue in your region? Who are your target customers? (e.g., fleet operators, fuel stations, wholesalers) Will you operate as a local supplier or aim for export? What are the regulatory and certification requirements in your market? Industry Insight: According to market research, the global demand for Diesel Exhaust Fluid (DEF) is projected to grow significantly in the coming years. Countries such as Turkey, Germany, India, and the UAE are witnessing a rapid increase in AdBlue consumption. Step 3: Location and Infrastructure Planning The success of your AdBlue production plant also depends on strategic decisions related to physical infrastructure. Site Selection Criteria: Access to raw materials: Ensure easy supply of technical-grade urea and deionized water. Transport logistics: Consider proximity to distribution channels (highways, ports, etc.). Utility availability: Stable electricity, clean water, and drainage are critical. Zoning and compliance: Make sure the property complies with industrial regulations. You’ll also need space for: Blending and mixing area Storage tanks for raw materials and finished AdBlue Filling and packaging lines Laboratory or testing room Loading/unloading zones Office/admin space Step 4: Choosing the Right Production Technology The heart of your plant is the AdBlue production line—and selecting the right technology will affect your efficiency, cost, and product quality. Main Components of an AdBlue Production Line: Blending Unit Mixes urea and deionized water precisely (ISO 22241-compliant) Typically features conductivity sensors, heating jackets, and automated control Storage Tanks Made of stainless steel or HDPE (High-Density Polyethylene) Must be non-reactive and UV-resistant Filling Machines Available for various volumes: 5L, 10L, 20L cans, 200L drums, and 1000L IBC tanks Can be manual, semi-automatic, or fully automatic Labeling and Capping Important for compliance, branding, and traceability Quality Control Equipment Inline monitoring systems for density, pH, and conductivity Laboratory kits for batch testing Production Capacity Options: Small scale: 500–1000 liters/hour (ideal for startups) Medium scale: 1000–5000 liters/hour Large scale: 5000+ liters/hour (for exporters and big distributors) Atmosfer Makina specializes in all capacity levels, offering scalable systems tailored to client needs. Step 5: Partnering with a Turnkey AdBlue Plant Provider Instead of sourcing each component individually, working with a single solution provider like Atmosfer Makina simplifies your setup. With expertise in machinery design, automation, and international standards, they offer: Complete AdBlue production line setup Custom plant layout and engineering design Installation and commissioning Operator training Remote monitoring and support Step 6: Legal & Environmental Compliance AdBlue is a chemically sensitive product regulated under ISO 22241 standards. To ensure compliance: Source technical-grade urea (ISO 22241-1 compliant) Use demineralized or deionized water Equip your facility with spill containment systems Perform batch testing and maintain quality control logs Label packaging correctly (include batch number, expiry date, usage instructions) Environmental licenses and safety audits may also be required depending on your location. Step 7: Setting Up Utilities and Support Systems A production facility doesn’t just run on machines—it needs a range of supporting infrastructure. Essential Utility Systems: Water Treatment Unit: RO systems to ensure deionized water Air Compressor: For pneumatic controls and valves Electrical Panel: To manage automation and power distribution CIP System (Clean-In-Place): For sanitary cleaning of mixing tanks and pipes Temperature Control System: Heating and insulation for optimal production Step 8: Staff Recruitment & Training Even with a fully automated line, human expertise is vital. Key Personnel: Production Supervisor Maintenance Technician Quality Control Analyst Warehouse/Logistics Staff Admin/Compliance Manager Atmosfer Makina provides hands-on training for your operators, including: Machine operation Troubleshooting Routine maintenance Emergency protocols Step 9: Launch and Operational Scaling Once your plant is installed and certified, it’s time to launch operations. But that’s just the beginning. First Production Run: Test small batches Validate lab results Package and label for internal evaluation Collect feedback and make adjustments Scaling Up: Gradually increase production hours Invest in additional storage or filling units Expand distribution networks Marketing your AdBlue brand and ensuring reliable logistics will become your next major focus. Ready to Build Your AdBlue Production Line? Cost Breakdown Maintenance & Optimization Tips Marketing & Distribution Strategy ❓ Frequently Asked Questions (FAQ) What are the basic requirements to set up an AdBlue production line? You will need access to high-purity urea, deionized water, adequate space for equipment installation, and a reliable power
Meet Atmosfer Makina at Automechanika Istanbul 2025: Explore Next-Gen AdBlue Production Line Solutions
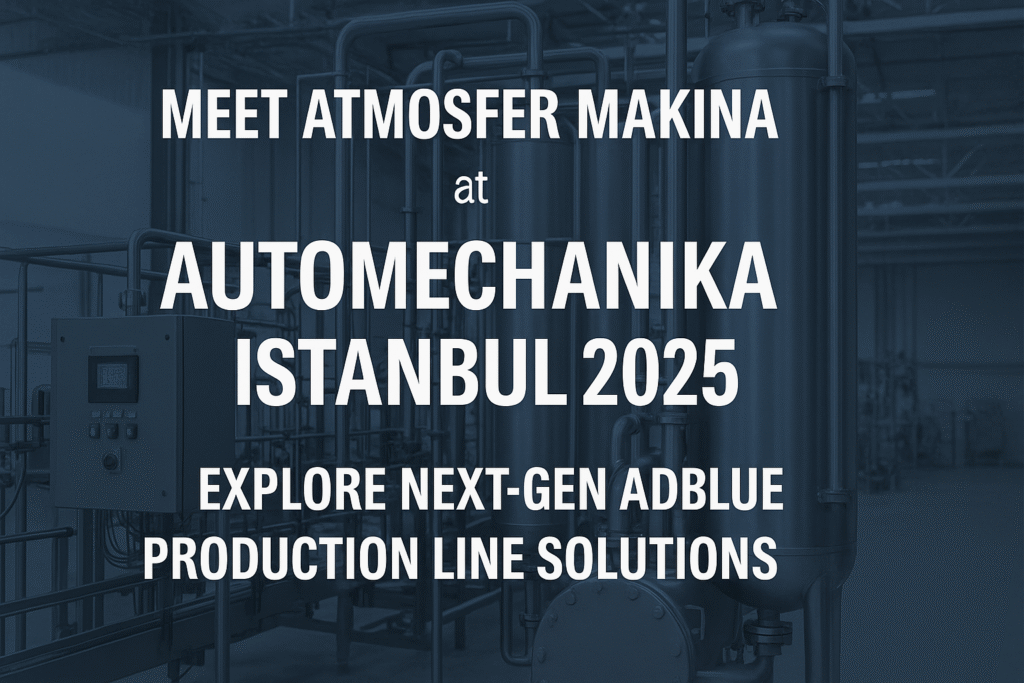
Discover Atmosfer Makina at Automechanika Istanbul 2025, showcasing next-gen AdBlue production line solutions. From turnkey AdBlue plants in Turkey to innovative DEF technologies—join us at the global expo for cleaner fuel production. Automechanika Istanbul 2025 stands as one of the most anticipated automotive trade shows of the year. Taking place from May 8–11, 2025, at the TÜYAP Fair and Congress Center, the event connects automotive professionals across Europe, Asia, and the Middle East. With more than 1,400 exhibitors and over 50,000 visitors expected, this international platform offers the perfect stage for manufacturers, suppliers, and technology leaders to unveil their latest innovations. Among the top exhibitors this year is Atmosfer Makina, a leading AdBlue production line manufacturer from Turkey. Known for delivering advanced machinery and turnkey AdBlue plant solutions, the company brings its engineering excellence and customer-centric approach to the forefront of the DEF (Diesel Exhaust Fluid) industry. Attendees can expect to explore high-efficiency production systems designed to meet the growing global demand for environmentally compliant fuel additives. Why Automechanika Matters for the AdBlue Industry With environmental regulations tightening across global markets, the need for efficient, scalable, and sustainable AdBlue production is stronger than ever. AdBlue, also known as Diesel Exhaust Fluid (DEF), is a urea-based solution used to reduce nitrogen oxide (NOx) emissions from diesel engines. As the automotive industry pivots toward cleaner and more eco-conscious practices, companies involved in AdBlue manufacturing play a critical role in ensuring regulatory compliance and air quality improvement. Automechanika Istanbul 2025 provides a timely platform for companies like Atmosfer Makina to showcase how innovative technology can support these objectives. As an AdBlue equipment supplier Turkey with a growing international reputation, Atmosfer Makina is set to demonstrate how intelligent automation, modular systems, and IoT-enabled solutions are transforming DEF production. Meet Atmosfer Makina: Innovation, Quality, and Global Reach Founded with a mission to provide high-performance industrial solutions, Atmosfer Makina has become a trusted name in the DEF and AdBlue industry. Specializing in machinery design, manufacturing, and integration, the company offers complete production lines for AdBlue blending, storage, filling, labeling, and packaging. Core Competencies AdBlue blending and packaging systems Designed to ensure ISO 22241 compliance and minimize impurities, these systems provide accurate mixing ratios and consistent product quality. Custom turnkey AdBlue plants From compact, containerized units to fully automated production facilities, Atmosfer Makina delivers bespoke setups tailored to the client’s location, capacity, and operational goals. Smart automation and data systems Their production lines feature modern monitoring interfaces, enabling users to remotely control and analyze the performance of their AdBlue systems in real time. Export-ready machinery With CE and ATEX certifications, Atmosfer Makina’s equipment meets the rigorous standards required for distribution in Europe, the Middle East, Africa, and Asia. As a result, Atmosfer Makina has earned a solid reputation not only as a machinery producer but also as a DEF production line expo Istanbul highlight. Their participation in Automechanika 2025 marks a strategic effort to expand global partnerships, explore new markets, and demonstrate their competitive edge. What Visitors Can Expect at the Atmosfer Makina Booth At Automechanika Istanbul 2025, Atmosfer Makina’s exhibition stand will be more than just a product showcase—it will be a hub for innovation, collaboration, and future-focused technology. Attendees will have the opportunity to: Witness real-time machine demonstrations See how automated blending, filling, and packaging systems work together to deliver seamless AdBlue production processes. Engage in live Q&A with technical experts Atmosfer Makina’s engineering team will be available to discuss production challenges, technical needs, and project feasibility. Explore customizable solutions Whether for high-volume plants or portable production modules, the stand will present flexible configurations to meet diverse business needs. Receive exclusive brochures and digital resources Visitors can take home or download full technical catalogs, setup diagrams, and system configuration samples for further exploration. For those interested in clean fuel technology, industrial automation, or expanding into the AdBlue market, this is a must-visit booth. With growing demand in both developed and emerging economies, Atmosfer Makina’s intelligent machinery is positioned as a cornerstone of next-generation fuel systems. A Word from the Founder “Participating in Automechanika Istanbul is more than a business opportunity—it’s a chance to connect with visionaries who are shaping the future of the automotive and clean fuels industry,” says the founder of Atmosfer Makina. “We’re proud to present our latest AdBlue solutions and demonstrate how turnkey efficiency, compliance, and sustainability can go hand-in-hand.” Cutting-Edge Technology Behind Atmosfer Makina’s AdBlue Solutions As the global demand for cleaner fuel additives grows, manufacturers are seeking not only quality equipment but also long-term operational efficiency. Atmosfer Makina has addressed this industry need by developing some of the most advanced and user-friendly AdBlue blending and packaging systems on the market. Designed with flexibility, precision, and durability in mind, these systems represent a new standard for DEF (Diesel Exhaust Fluid) production lines. Whether you’re launching a small production unit or managing a large-scale facility, Atmosfer Makina offers modular configurations that suit all business sizes. Their in-depth engineering approach ensures that every machine aligns with both local regulations and global standards like ISO 22241. Comprehensive Product Range for AdBlue Production Atmosfer Makina offers a full suite of AdBlue manufacturing equipment, including: Blending Units These automated systems mix urea and deionized water with exact ratios, ensuring homogeneity and chemical stability. The machines are equipped with: Real-time conductivity and density sensors Anti-corrosive internal surfaces Automated mixing algorithms with fail-safes This allows production managers to maintain consistency across batches while optimizing input usage and minimizing waste. Filling and Capping Machines Available in multiple capacity models—from 5L jerrycans to 1000L IBC tanks—these machines are tailored for precision dosing and high-speed operation. Features include: Servo-driven filling valves for low tolerance levels Anti-drip mechanisms to maintain cleanliness Quick changeover options for different packaging sizes Labeling Systems Using high-resolution print-and-apply technology, Atmosfer Makina’s labeling units ensure regulatory compliance and professional presentation. Benefits include: Variable data printing (batch numbers, dates) Multilingual label support RFID/NFC tag integration (optional) Inline Quality Control Modules These smart stations verify
Diesel Exhaust Fluid Plant Setup: Tips for Maximum Efficiency

Understanding the Importance of a Diesel Exhaust Fluid Plant A diesel exhaust fluid plant is essential for producing DEF, a solution critical for reducing nitrogen oxide emissions in diesel engines. These plants play a significant role in ensuring that diesel vehicles meet stringent environmental regulations while maintaining optimal engine performance. Establishing a well-designed diesel exhaust fluid plant enables businesses to produce high-quality DEF efficiently, ensuring compliance with ISO 22241 standards and supporting sustainability goals. Choosing the Right Location Location is a crucial factor when setting up a diesel exhaust fluid plant. The site should have sufficient space for production equipment, storage tanks, and logistics operations. Proximity to transportation routes and raw material suppliers further enhances operational efficiency. When planning your diesel exhaust fluid plant, consider accessibility for distribution networks. A well-connected location reduces transportation costs and ensures timely delivery of DEF to clients. Essential Equipment for DEF Production A fully operational diesel exhaust fluid plant requires specific equipment, including mixing tanks, deionized water systems, and automated blending machines. These components are critical for producing DEF that meets strict quality standards. Investing in advanced equipment ensures precise urea-water blending and minimizes production errors. This enhances the efficiency and reliability of your diesel exhaust fluid plant. Maintaining Quality Standards Quality control is vital in a diesel exhaust fluid plant. Regular testing of urea concentration and water purity ensures the DEF complies with ISO standards. Advanced monitoring tools help maintain consistency in every batch. Implementing strict quality assurance protocols reduces the risk of producing substandard DEF. A focus on quality not only protects diesel engines but also builds trust with customers and partners. Optimizing Energy Usage Energy efficiency is a key consideration when running a diesel exhaust fluid plant. Using energy-efficient equipment and optimizing production processes can significantly reduce operational costs. Incorporating renewable energy sources into your plant’s power supply further enhances sustainability. This approach supports both cost savings and environmental goals, making your diesel exhaust fluid plant more competitive in the market. Managing Raw Material Supply Securing a reliable supply of high-purity urea and deionized water is essential for the smooth operation of a diesel exhaust fluid plant. Establishing strong partnerships with reputable suppliers ensures consistent availability of raw materials. Effective inventory management reduces waste and prevents production disruptions. A well-managed supply chain is critical to the long-term success of your diesel exhaust fluid plant. Scaling Production for Growth A scalable diesel exhaust fluid plant allows businesses to adapt to increasing demand. Modular production systems enable seamless expansion without significant downtime or capital investment. Planning for scalability from the outset ensures your plant remains competitive in a growing market. A flexible production setup supports future growth and positions your diesel exhaust fluid plant for sustained success. Ensuring Safety and Compliance Safety is paramount in a diesel exhaust fluid plant. Adhering to safety regulations and implementing best practices minimizes risks for workers and the environment. Regular inspections and employee training are essential for maintaining a safe workplace. Compliance with local and international standards ensures your diesel exhaust fluid plant operates legally and ethically. This commitment to safety and compliance strengthens your reputation and enhances operational reliability. Conclusion Setting up a diesel exhaust fluid plant requires careful planning, investment in quality equipment, and adherence to strict standards. By focusing on efficiency, scalability, and sustainability, businesses can produce high-quality DEF while minimizing costs and environmental impact. With a well-designed plant, companies can meet growing demand and contribute to cleaner, more sustainable diesel operations. Frequently Asked Questions What is a diesel exhaust fluid plant? A facility designed to produce DEF by blending high-purity urea with deionized water according to ISO standards. Why is location important for a DEF plant? A well-located plant reduces transportation costs and ensures efficient distribution of DEF. What equipment is essential for DEF production? Key components include mixing tanks, deionized water systems, and automated blending machines. How can I maintain quality standards in a DEF plant? Regular testing and monitoring ensure the DEF complies with ISO standards and maintains consistency. Is scaling production possible in a DEF plant? Yes, modular systems allow for easy expansion as demand grows, ensuring the plant remains competitive. What safety measures are needed in a DEF plant? Regular inspections, employee training, and adherence to safety standards minimize risks and ensure compliance. How can energy efficiency be improved in a DEF plant? Using energy-efficient equipment and incorporating renewable energy sources reduces costs and environmental impact.
Inside the World of Diesel Exhaust Fluid Manufacturers
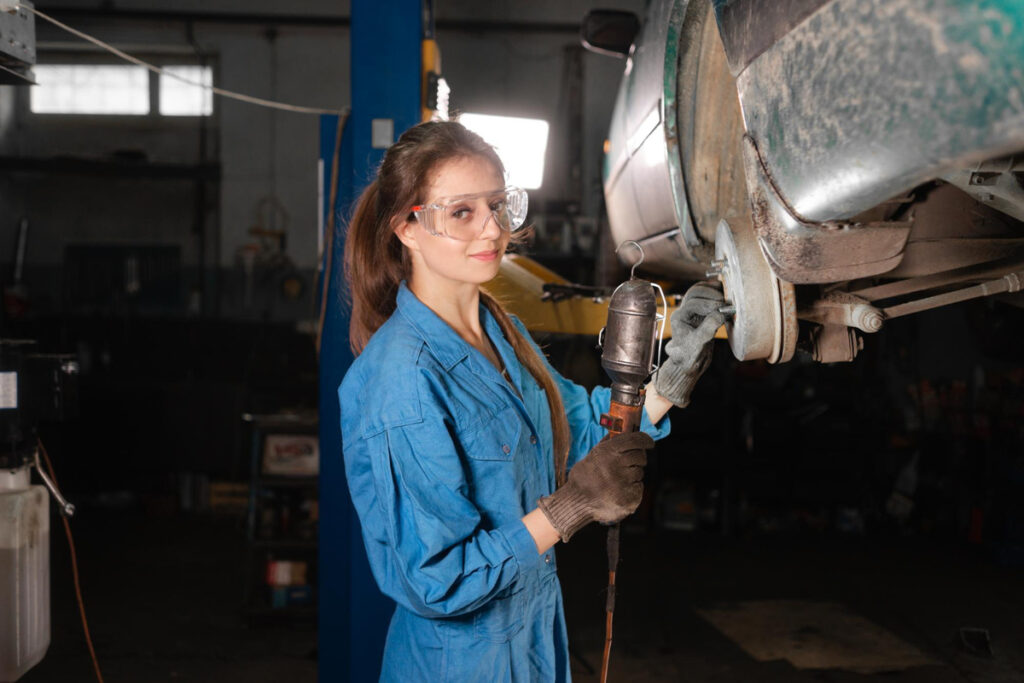
Who Are Diesel Exhaust Fluid Manufacturers? Diesel exhaust fluid manufacturers are essential players in the automotive and industrial sectors. They produce DEF, a non-toxic solution critical for reducing harmful nitrogen oxide emissions in diesel engines equipped with Selective Catalytic Reduction (SCR) systems. These manufacturers are responsible for ensuring that DEF meets strict ISO 22241 standards, maintaining product quality, and supporting global efforts to combat air pollution. Without reliable diesel exhaust fluid manufacturers, compliance with environmental regulations would be challenging. The Role of DEF in Modern Industries DEF plays a pivotal role in enabling diesel engines to meet stringent emission standards. By breaking down nitrogen oxides into harmless nitrogen and water, DEF helps reduce air pollution and supports sustainable practices in transportation and industrial operations. Diesel exhaust fluid manufacturers cater to a wide range of industries, including logistics, agriculture, and construction, providing them with the essential fluid needed to keep their operations compliant and efficient. Key Components of DEF Production The production process for DEF involves blending high-purity urea with deionized water. Diesel exhaust fluid manufacturers must maintain precise urea concentrations to meet industry standards and ensure product effectiveness. Advanced equipment, such as automated blending systems and quality control tools, is used to produce DEF consistently. This ensures that the fluid meets the stringent requirements necessary for SCR systems to function effectively. Challenges Faced by Diesel Exhaust Fluid Manufacturers Diesel exhaust fluid manufacturers face various challenges, including fluctuating raw material costs, regulatory compliance, and maintaining consistent quality. These challenges require innovative solutions and constant adaptation to industry changes. Additionally, the growing demand for DEF puts pressure on manufacturers to scale their operations while maintaining high standards. This requires significant investment in technology and infrastructure. Innovations in DEF Manufacturing Technological advancements have revolutionized the production process for DEF. Automated systems now allow diesel exhaust fluid manufacturers to produce large quantities of DEF efficiently while minimizing waste. Innovations such as real-time quality monitoring and improved energy-efficient processes further enhance the production capabilities of diesel exhaust fluid manufacturers, ensuring their products remain competitive in the market. Environmental Impact of DEF Production DEF production contributes to global sustainability by enabling diesel engines to reduce their emissions. Diesel exhaust fluid manufacturers play a critical role in promoting cleaner air and supporting industries in meeting their environmental goals. Many manufacturers are also adopting eco-friendly practices within their facilities, such as using renewable energy sources and minimizing water waste, to align with broader sustainability objectives. Meeting the Growing Demand for DEF The demand for DEF continues to rise due to stricter emission regulations and increased adoption of SCR systems. Diesel exhaust fluid manufacturers are scaling their production capabilities to meet this growing need while maintaining consistent quality. Expanding production facilities and improving logistics networks are essential strategies for manufacturers to ensure a steady supply of DEF to their customers, even in remote locations. The Future of Diesel Exhaust Fluid Manufacturing The future of DEF manufacturing lies in continuous innovation and sustainability. Diesel exhaust fluid manufacturers are expected to invest in advanced technologies and streamline production processes to stay ahead in a competitive market. As emission standards become more stringent, the demand for DEF will only increase. Manufacturers that prioritize quality, efficiency, and environmental responsibility will lead the way in this evolving industry. Conclusion Diesel exhaust fluid manufacturers are vital for enabling diesel engines to meet emission standards and supporting industries in their sustainability efforts. By overcoming challenges, embracing innovations, and scaling operations, these manufacturers continue to provide high-quality DEF to meet the growing global demand. Their role in promoting cleaner air and sustainable practices underscores their importance in the modern industrial landscape. Frequently Asked Questions What is DEF? DEF, or Diesel Exhaust Fluid, is a solution of urea and deionized water used to reduce emissions in diesel engines. Who are diesel exhaust fluid manufacturers? They are companies that produce DEF, ensuring it meets ISO standards for use in SCR systems. Why is quality important in DEF production? High-quality DEF ensures effective emission reduction and prevents damage to diesel engines. What challenges do DEF manufacturers face? They face challenges like fluctuating raw material costs, regulatory compliance, and growing demand. How do manufacturers ensure DEF quality? Through advanced quality control tools and regular testing of urea concentration and water purity. Is DEF production environmentally friendly? Yes, it supports emission reduction and promotes cleaner air by enabling diesel engines to comply with regulations. What innovations are shaping DEF manufacturing? Automation, real-time quality monitoring, and energy-efficient processes are key innovations in DEF production.
Make Your Own DEF Fluid: Cost-Effective Solutions for Companies
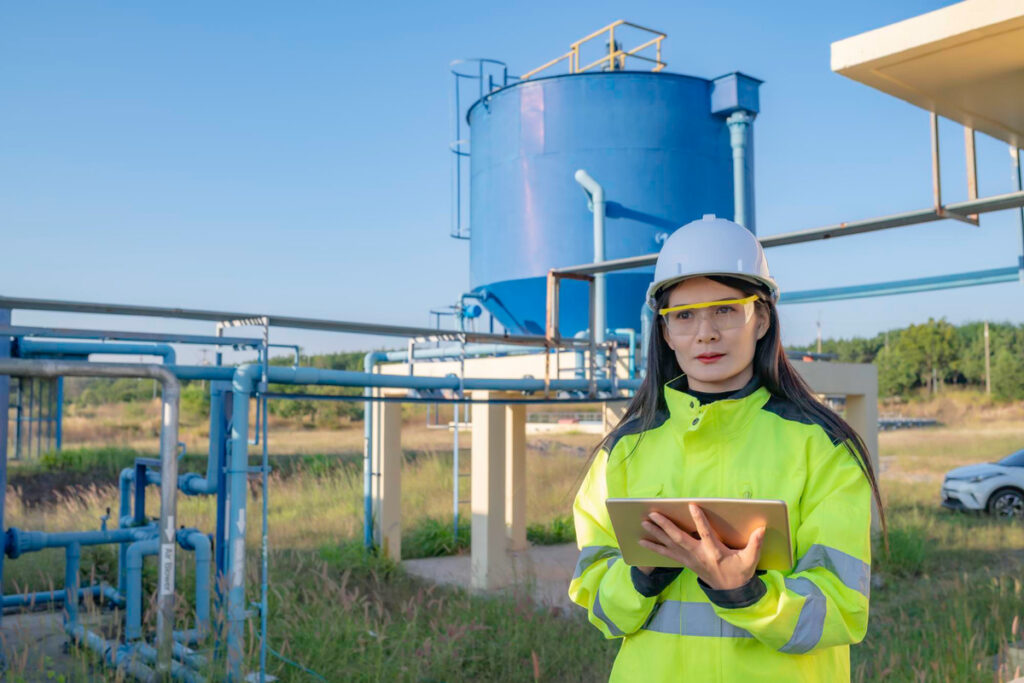
Why Consider Making Your Own DEF Fluid? For companies relying on diesel-powered vehicles, the ability to make your own DEF fluid offers significant advantages. DEF, or Diesel Exhaust Fluid, is essential for reducing harmful nitrogen oxide emissions and complying with environmental regulations. Establishing an in-house DEF production system helps businesses cut costs, maintain a steady supply, and ensure product quality. These benefits make the decision to make your own DEF fluid a strategic move for long-term sustainability. Key Benefits of Producing DEF In-House Choosing to make your own DEF fluid allows companies to save on purchasing and logistics costs. Outsourcing DEF can become expensive due to fluctuating supplier prices and transportation fees. Producing DEF internally eliminates these variables. Additionally, having control over production ensures the DEF meets ISO standards, protecting diesel engines from potential damage. This control enhances reliability and builds trust with fleet operators who rely on the product. Essential Equipment for DEF Production Setting up a DEF production system requires specialized equipment. Key components include mixing tanks, deionized water systems, and automated blending machines. These tools ensure precise mixing of urea and water to produce high-quality DEF. For businesses planning to make your own DEF fluid, investing in advanced technology improves efficiency and reduces waste, resulting in cost-effective operations. How to Source High-Quality Materials To make your own DEF fluid, sourcing high-purity urea and deionized water is critical. These raw materials determine the quality and effectiveness of the final product. Partnering with reputable suppliers ensures consistency and compliance with standards. Using inferior materials can lead to substandard DEF, which may damage SCR systems and result in costly repairs. High-quality inputs are essential for maintaining product integrity and customer satisfaction. Steps to Start Your DEF Production The process to make your own DEF fluid begins with setting up the production site. The facility should have adequate space for equipment, storage tanks, and future expansion. Once the infrastructure is in place, install the necessary machinery and perform initial testing. During production, high-purity urea is blended with deionized water in precise ratios. Automated systems ensure the DEF meets ISO 22241 standards, making it safe for use in diesel engines. Quality control testing follows to verify the product’s compliance. Cost Analysis: Saving with In-House Production One of the primary reasons to make your own DEF fluid is cost efficiency. By producing DEF internally, companies eliminate the need for external suppliers and reduce transportation expenses. This approach can result in significant savings, especially for businesses with large fleets. Additionally, investing in reliable equipment reduces operational costs over time. A well-maintained system ensures consistent production without unexpected expenses, further enhancing cost-effectiveness. Environmental Impact of DEF Production Producing DEF in-house contributes to sustainability efforts by reducing emissions and minimizing transportation-related pollution. Companies that make your own DEF fluid actively participate in creating cleaner air and meeting global environmental goals. Modern DEF production systems are designed to minimize waste and optimize resource usage, aligning with corporate social responsibility objectives. This commitment to sustainability enhances a company’s reputation in the marketplace. Scalability for Growing Businesses For businesses considering how to make your own DEF fluid, scalability is a critical factor. Modular production systems allow for easy expansion as demand grows. This adaptability ensures companies can meet market needs without significant delays. Planning for future growth during the initial setup of DEF production ensures the business remains competitive and capable of responding to increased demand effectively. Conclusion Deciding to make your own DEF fluid offers numerous benefits for businesses, including cost savings, quality control, and environmental sustainability. By investing in the right equipment and sourcing high-quality materials, companies can establish efficient production systems that meet industry standards. In-house DEF production positions businesses for long-term success and enhances their commitment to cleaner emissions. Frequently Asked Questions What is DEF? DEF, or Diesel Exhaust Fluid, is a solution made of urea and deionized water used to reduce emissions in diesel engines. Why should I make my own DEF fluid? Producing DEF in-house offers cost savings, quality control, and a reliable supply for your operations. What equipment is needed for DEF production? Essential equipment includes mixing tanks, deionized water systems, and automated blending machines. How do I ensure my DEF meets standards? Regular testing and sourcing high-quality raw materials ensure your DEF complies with ISO 22241 standards. What are the cost benefits of in-house DEF production? In-house production eliminates supplier and transportation costs, resulting in significant savings. Is DEF production environmentally friendly? Yes, DEF reduces emissions and helps companies align with sustainability goals. Can DEF production systems be scaled? Yes, modular systems allow businesses to expand production capacity as demand grows.